What Is the Role of Post-Processing in UV Flatbed Printing?
What Is the Role of Post-Processing in UV Flatbed Printing?
UV flatbed printing has revolutionized the printing industry, offering unparalleled versatility, precision, and efficiency. This technology allows for direct printing onto a wide range of substrates, from rigid materials like glass and metal to flexible ones like vinyl and fabric. However, the printing process does not end when the UV ink hits the substrate. Post-processing plays a crucial role in enhancing the final output, ensuring durability, and adding value to the printed products. In this article, we delve into the significance of post-processing in UV flatbed printing, exploring its various stages, benefits, and the techniques employed.
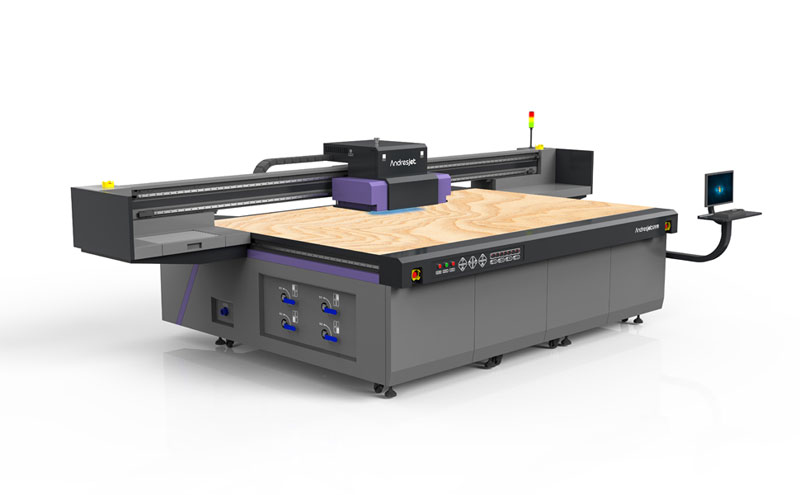
Understanding UV Flatbed Printing
Before we dive into post-processing, it is essential to grasp the basics of UV flatbed printing. This method utilizes ultraviolet (UV) curable inks that are instantly dried and cured by UV light as soon as they are applied to the substrate. This immediate curing process eliminates the need for drying time, enabling faster production speeds and immediate handling of the printed materials. UV flatbed printers can print on substrates of varying thicknesses and sizes, making them ideal for a diverse range of applications, including signage, packaging, artistic reproductions, and more.
The Importance of Post-Processing
While UV flatbed printing offers numerous advantages, the quality and longevity of the prints can be significantly enhanced through post-processing. Post-processing encompasses a series of steps designed to refine the printed output, improve its durability, and, in some cases, add functional features. Here are the key aspects of post-processing in UV flatbed printing:
1. Curing and Drying
Although UV inks cure instantly upon exposure to UV light, a secondary curing process can further enhance their adhesion and durability. This additional curing step ensures that the inks are fully polymerized, reducing the risk of ink cracking, fading, or peeling over time. It also helps to eliminate any residual odors from the inks, making the prints more suitable for indoor applications.
2. Lamination
Lamination is a common post-processing technique that involves applying a thin, transparent film over the printed surface. This film provides a protective layer, shielding the print from scratches, abrasions, and environmental factors such as moisture and UV rays. Lamination can be glossy, matte, or textured, depending on the desired finish and level of protection required. It not only enhances the durability of the print but also adds a professional touch, improving its overall aesthetic appeal.
3. Cutting and Trimming
Precision cutting and trimming are vital for achieving clean edges and ensuring that the printed materials fit their intended applications perfectly. UV flatbed printers often come equipped with cutting systems that can accurately trim the prints to the desired dimensions. For more intricate designs, die-cutting may be employed, allowing for detailed shapes and contours to be cut out of the printed materials.
4. Mounting and Framing
For larger prints or those intended for display purposes, mounting and framing are crucial steps. Mounting involves adhering the print to a rigid substrate, such as foam board, plywood, or aluminum, to provide stability and support. Framing, on the other hand, adds a finished look and can further protect the print from damage. Both processes are particularly important in applications like gallery exhibitions, trade show displays, and interior decor.
5. Varnishing and Spot UV
Varnishing adds a layer of clear, protective coating to the print, enhancing its color saturation and providing a smooth, glossy finish. Spot UV, on the other hand, involves applying UV varnish to specific areas of the print, creating a contrast between the matte and glossy sections. This technique can be used to highlight key elements of the design, add depth, and create a visually striking effect.
6. Embossing and Debossing
Embossing and debossing are techniques that involve raising or depressing specific areas of the print to create a tactile effect. Embossing adds a three-dimensional quality to the design, making it more engaging and interactive. Debossing, conversely, creates a recessed area, adding depth and texture to the print. These techniques are often used in high-end printing applications, such as luxury packaging and invitations, to convey a sense of sophistication and exclusivity.
Benefits of Post-Processing
The post-processing steps outlined above offer several benefits that contribute to the overall success of UV flatbed printing projects:
Enhanced Durability: By protecting the prints from environmental factors and physical wear and tear, post-processing ensures that they last longer and maintain their quality over time.
Improved Aesthetics: Techniques like lamination, varnishing, and spot UV enhance the visual appeal of the prints, making them more attractive and professional.
Added Functionality: Post-processing can add functional features, such as waterproofing or scratch resistance, making the prints suitable for a wider range of applications.
Versatility: The ability to customize post-processing steps allows for greater flexibility in meeting the specific requirements of each project, whether it’s a simple poster or a complex packaging design.
Increased Value: By elevating the quality and durability of the prints, post-processing adds value to the final product, making it more appealing to clients and end-users.
Conclusion
Post-processing is an integral part of UV flatbed printing, playing a critical role in enhancing the quality, durability, and aesthetic appeal of the prints. From curing and lamination to cutting, mounting, and embossing, each step contributes to the overall success of the printing project. By investing time and resources into post-processing, printers can ensure that their UV flatbed prints not only meet but exceed client expectations, standing the test of time and showcasing the full potential of this innovative printing technology.
In essence, post-processing is the unsung hero of UV flatbed printing, working behind the scenes to transform raw prints into finished products that are both visually stunning and functionally superior. As the printing industry continues to evolve, so too will the post-processing techniques, pushing the boundaries of what is possible with UV flatbed printing and opening up new avenues for creativity and innovation.