UV Flatbed Printers: Understanding UV-Curable Ink Technology
UV Flatbed Printers: Understanding UV-Curable Ink Technology
UV flatbed printers have revolutionized the printing industry, offering unparalleled versatility, precision, and efficiency. At the heart of this technological marvel lies UV-curable ink—a sophisticated medium that sets these printers apart from traditional printing systems. This article delves into the intricacies of UV-curable ink technology, exploring its composition, working mechanisms, benefits, and applications in UV flatbed printers.
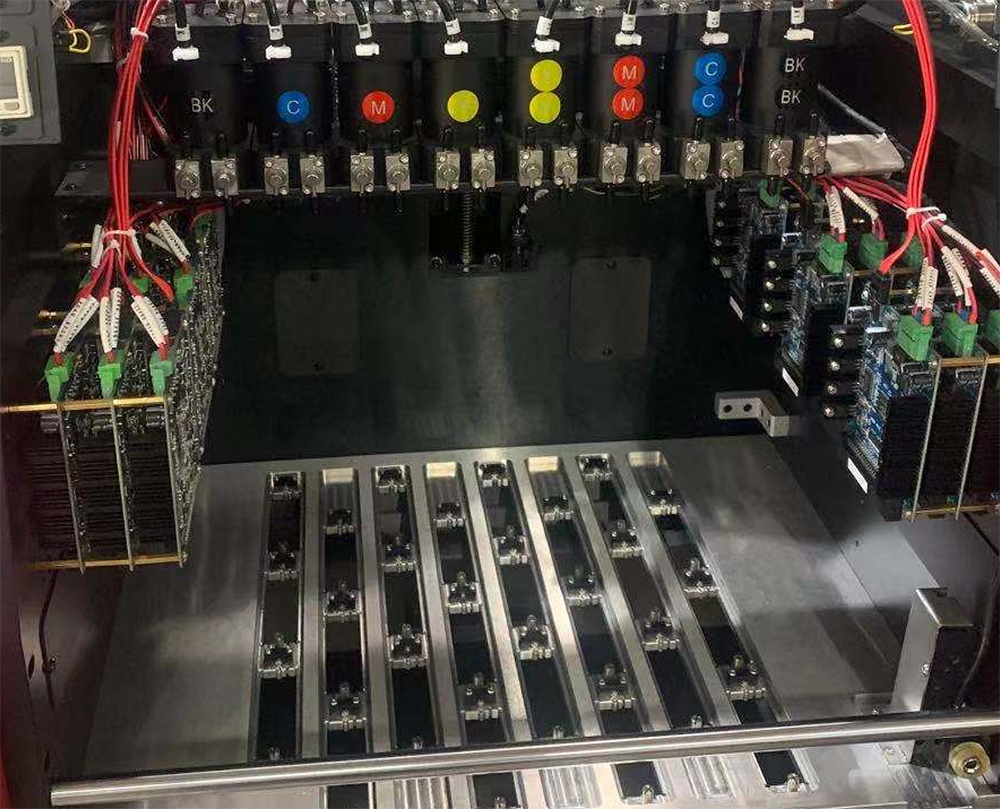
Introduction to UV Flatbed Printers
UV flatbed printers are advanced digital printing machines capable of printing directly onto a wide range of materials, including rigid substrates such as metal, glass, wood, plastic, and even flexible media like fabrics and leather. Unlike conventional printers that rely on solvent-based or water-based inks, UV flatbed printers utilize UV-curable inks that solidify instantly when exposed to ultraviolet light. This unique feature enables them to produce high-quality prints with exceptional durability and vibrant colors.
The Science Behind UV-Curable Ink
Composition of UV-Curable Inks
UV-curable inks are formulated using a complex blend of components, each serving a specific purpose:
Pigments or Dyes: These provide the color to the ink. Pigments are preferred for their durability and resistance to fading.
Binders: Also known as oligomers or resins, they form the backbone of the ink film after curing. They ensure adhesion to the substrate and provide mechanical strength.
Monomers: These are low-viscosity liquids that help in the fluidity of the ink during jetting and aid in the polymerization process.
Photoinitiators: These are chemicals that absorb UV light and initiate the cross-linking reaction between the binder and monomers, leading to curing.
Additives: These include flow agents, stabilizers, and other modifiers to enhance the ink’s performance and printability.
How UV-Curable Inks Work
The printing process in UV flatbed printers involves several critical steps:
Ink Jetting: The printer’s printhead, often utilizing piezoelectric or thermal technology, ejects droplets of UV-curable ink onto the substrate. This can be done in a single pass or through multiple layers for enhanced color depth and texture.
UV Curing: Immediately after ink deposition, the printed area is exposed to high-intensity UV light. This light activates the photoinitiators in the ink, triggering a chemical reaction known as polymerization. During this process, the monomers and oligomers cross-link to form a solid, durable film.
Post-Curing (Optional): In some cases, an additional curing step using stronger UV light or a different wavelength may be employed to ensure complete curing, especially for thicker ink layers or deep cures.
Benefits of UV-Curable Ink Technology
1. Instant Curing
The rapid curing of UV-inks eliminates the need for lengthy drying times, significantly boosting productivity. Prints are ready for further handling or processing immediately after curing, reducing turnaround times.
2. Enhanced Durability
UV-cured inks form a strong, flexible, and abrasion-resistant film that adheres well to a variety of substrates. This results in prints that are highly resistant to fading, chemicals, and environmental factors such as moisture and temperature changes.
3. Versatility in Substrate Compatibility
Unlike traditional inks that may be limited to specific surfaces, UV-curable inks can bond to a wide range of materials, including non-absorbent and heat-sensitive substrates. This versatility makes UV flatbed printers ideal for diverse applications.
4. High-Resolution Prints
The precise control over ink deposition allows for high-resolution printing, achieving intricate details and smooth gradients. This is crucial for applications requiring fine artwork, such as graphic design, photography, and product labeling.
5. Environmental Advantages
UV-curable inks are often more environmentally friendly than solvent-based alternatives. They emit no volatile organic compounds (VOCs) during curing, contributing to a cleaner and safer printing environment.
6. Cost-Effective
Although the initial investment in a UV flatbed printer may be higher, the long-term benefits—including reduced ink waste, minimal maintenance, and higher productivity—can lead to significant cost savings.
Applications of UV Flatbed Printers
1. Signage and Display Graphics
UV flatbed printers excel in producing vibrant, durable graphics for indoor and outdoor signage. Whether it’s large-format banners, backlit signs, or point-of-purchase displays, UV-cured inks ensure longevity and visual appeal.
2. Industrial Printing
In the industrial sector, UV flatbed printers are used for printing on components, panels, and machinery. They can print functional features such as serial numbers, barcodes, and instructional graphics directly onto the product, enhancing efficiency and traceability.
3. Decorative Printing
From customizing automotive parts to decorating furniture and interior design elements, UV flatbed printers offer limitless creative possibilities. The ability to print on various materials allows for innovative designs and finishes.
4. Packaging
UV-curable inks are ideal for packaging applications, providing high-quality prints that withstand the rigors of handling, shipping, and storage. They can be used for branding, product information, and security features like QR codes.
5. Fine Art and Photography
Artists and photographers leverage UV flatbed printers to reproduce their work on various media, including canvas, metal, and acrylic. The precision and color accuracy of these printers ensure that the artistic vision is faithfully reproduced.
6. Textile and Apparel
Although traditional screen printing is still prevalent in textile printing, UV flatbed printers are increasingly being used for custom designs and short runs. They allow for direct printing on fabrics, offering vibrant colors and intricate patterns.
Challenges and Considerations
While UV-curable ink technology offers numerous advantages, it also presents certain challenges:
Initial Investment: The cost of UV flatbed printers and the associated UV curing systems can be high.
Ink Costs: UV-curable inks are generally more expensive than conventional inks, although their efficiency and durability can offset this.
Operator Training: Proper handling and maintenance of UV flatbed printers require specialized knowledge and training.
Health and Safety: Exposure to UV light and certain ink components can pose health risks, necessitating proper safety measures.
Future Trends
The UV printing market is continually evolving, with ongoing advancements in ink formulations, printhead technology, and curing systems. Trends to watch include:
Increased Automation: Integration with robotic systems for automated feeding, handling, and curing processes.
Multi-Functional Printers: Development of hybrid printers that combine UV printing with other technologies like laser cutting and engraving.
Sustainable Inks: Ongoing research into bio-based and recyclable UV-curable inks to further enhance environmental benefits.
Software Innovations: Advanced RIP (Raster Image Processor) software for optimized color management and print workflow.
UV flatbed printers with their UV-curable ink technology represent a significant advancement in the printing industry. They offer unparalleled versatility, precision, and efficiency, making them indispensable tools for a wide range of applications. Understanding the science behind UV-curable inks—their composition, curing mechanisms, and benefits—is crucial for harnessing the full potential of these innovative printers. As technology continues to evolve, UV flatbed printers will play an increasingly vital role in shaping the future of digital printing.