UV Flatbed Printer: Tips for Printing on Rigid Materials
UV flatbed printers have revolutionized the printing industry by enabling direct-to-substrate printing on rigid materials such as glass, metal, wood, acrylic, and ceramics. Unlike traditional methods that rely on vinyl wraps or transfers, UV printing applies ink directly to the material’s surface, curing it instantly with UV light. This process creates vibrant, durable, and high-resolution prints ideal for signage, displays, industrial labeling, and personalized décor. However, achieving flawless results on rigid materials requires careful preparation, technique, and troubleshooting. This article explores actionable tips for optimizing UV flatbed printing on rigid substrates, ensuring professional outcomes for businesses and hobbyists alike.
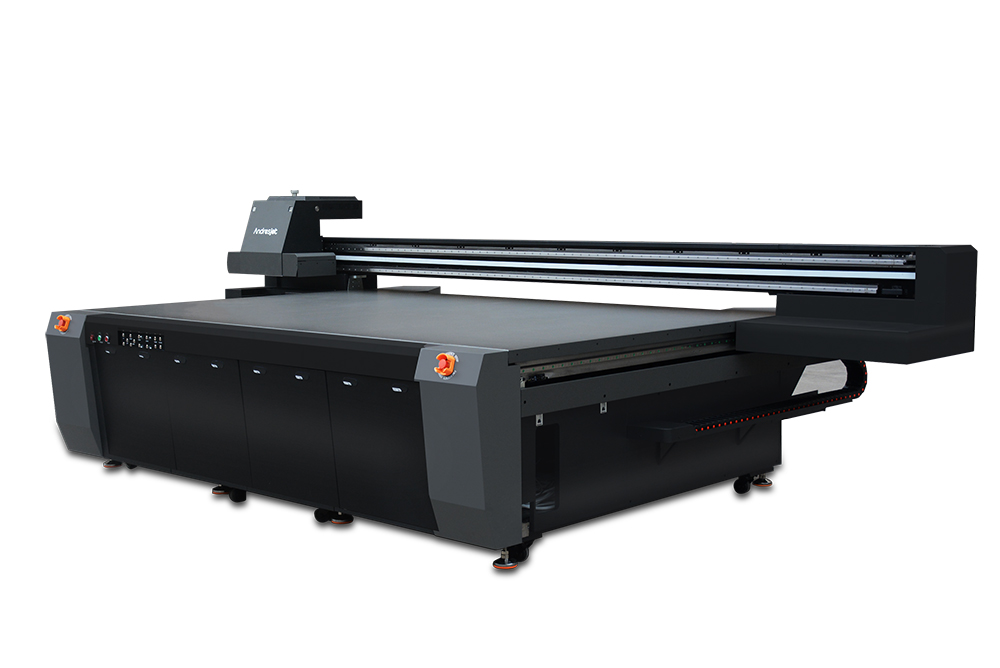
Understanding Rigid Materials and Their Challenges
Rigid materials differ significantly from flexible substrates like fabric or paper. Their hardness, porosity, and surface texture can affect ink adhesion, color accuracy, and print longevity. For example:
Glass and acrylic have smooth, non-porous surfaces that may repel ink if untreated.
Wood and metal may have uneven textures or coatings that hinder adhesion.
Ceramics and tiles require heat resistance and scratch-proof finishes.
To mitigate these challenges, users must assess the material’s composition, pre-treat it if necessary, and adjust printer settings accordingly. Testing small sections before full-scale production is crucial to avoid costly errors.
Surface Preparation: The Foundation of Success
Proper surface preparation is non-negotiable for UV printing on rigid materials. Skipping this step can lead to peeling, fading, or uneven color distribution. Here’s how to prepare common substrates:
Cleaning: Remove dust, oils, and contaminants using a lint-free cloth and isopropyl alcohol (70% or higher). For porous materials like wood, use compressed air to dislodge debris from crevices.
Sanding (for porous materials): Lightly sand wood or untreated metal to create micro-abrasions that improve ink grip. Wipe away residue afterward.
Priming (for tricky surfaces): Apply a UV-compatible primer to glass, acrylic, or glossy metals. These primers chemically bond with the ink, enhancing durability.
Static elimination: Use an anti-static brush or ionizer to prevent dust from adhering to the material during printing.
Pro Tip: Store materials in a clean, climate-controlled environment to avoid moisture absorption or warping.
Optimizing Printer Settings for Rigid Substrates
UV flatbed printers offer adjustable parameters to suit different materials. Mastering these settings ensures sharp details and vibrant colors:
Ink Curing: UV lamps must cure the ink thoroughly without overheating the substrate. Adjust lamp intensity and pass speed based on material thickness. Delicate materials like thin acrylic may require slower curing to prevent warping.
Print Height Adjustment: The printer’s vacuum table or z-axis controls the distance between the print head and the substrate. Set this gap to 2–3 mm for flat materials; thicker items like wooden plaques may need manual height calibration.
Drop Size and Resolution: Use smaller drop sizes (e.g., 4–7 picoliters) for fine details (e.g., photographs) and larger drops for solid color blocks. Higher resolutions (1440 dpi or above) enhance image quality but slow printing speed.
White Ink Layering: For transparent or dark materials, print a white ink base layer first to improve color opacity. Apply multiple thin coats rather than one thick layer to avoid cracking.
Pro Tip: Save custom profiles for frequently used materials to streamline workflows.
Design Considerations for Rigid Media
Designing for UV printing on rigid substrates demands attention to detail. Here’s how to ensure your artwork translates seamlessly to the final product:
Color Management: Use ICC profiles specific to your printer and substrate to maintain color accuracy. Avoid overly saturated hues, as UV inks may appear brighter than digital previews.
Bleed and Margins: Add a 2–3 mm bleed to designs that extend to the material’s edges to prevent white borders after trimming.
Text and Line Thickness: Ensure small text (below 8 pt) and thin lines (0.5 mm or wider) are bold enough to remain legible after curing.
3D Effects: Leverage layered printing to create textured finishes, such as embossed logos on metal or raised patterns on wood.
Pro Tip: Mock up designs on scaled physical samples to visualize how colors and textures will interact with the material.
Post-Printing Finishing Techniques
UV-printed rigid materials often require additional treatments to enhance durability or aesthetics:
Lamination: Apply a clear, scratch-resistant laminate to high-traffic items like floor graphics or outdoor signage.
Cutting and Shaping: Use a CNC router or laser cutter to trim printed panels into custom shapes. Ensure the material is fully cured before cutting to avoid ink smudging.
Mounting and Assembly: For multi-panel displays, use double-sided adhesive tape or mechanical fasteners. Avoid glue that may react with UV inks.
Weatherproofing: For outdoor use, seal edges with silicone caulk to prevent moisture ingress and add a UV-protective coating.
Pro Tip: Test finishing methods on spare material scraps to confirm compatibility with the printed surface.
Troubleshooting Common UV Printing Issues
Even experienced users encounter challenges. Here’s how to diagnose and fix common problems:
Ink Adhesion Failures: If prints peel or scratch easily, the material may lack proper pre-treatment. Re-clean the surface, apply primer, or adjust curing settings.
Banding or Streaking: Uneven ink distribution could stem from clogged print heads or incorrect vacuum table suction. Run a nozzle check and clean heads, or adjust table pressure.
Color Inconsistencies: Variations in ambient temperature or humidity may affect ink viscosity. Maintain a stable print environment (68–77°F, 40–60% humidity).
Curing Overheating: Warped acrylic or melted plastics indicate excessive UV exposure. Reduce lamp intensity or increase pass speed.
Pro Tip: Keep a log of print jobs, including material types, settings, and outcomes, to identify patterns and refine processes.
Expanding Possibilities: Creative Applications
UV flatbed printing opens doors to innovative projects beyond traditional signage:
Customized Home Décor: Print family photos on ceramic tiles, mandalas on wooden cutting boards, or galaxy scenes on acrylic partitions.
Industrial Branding: Add company logos to metal toolboxes, serialized labels to electronic components, or safety warnings to machinery panels.
Artistic Installations: Create large-scale murals on aluminum composite panels, backlit displays on frosted glass, or interactive exhibits on textured wood.
Pro Tip: Partner with local artists or designers to offer exclusive UV-printed products, tapping into niche markets.
Conclusion
UV flatbed printing on rigid materials empowers businesses and creatives to produce stunning, long-lasting products with minimal waste. By mastering surface preparation, printer calibration, design adjustments, and finishing techniques, users can unlock the full potential of this versatile technology. Whether crafting retail signage, personalized gifts, or industrial prototypes, attention to detail and a willingness to experiment will yield professional results. Start small, test rigorously, and scale your capabilities—the world of UV printing on rigid substrates awaits your creativity.