UV Flatbed Printer: Tips for Printing on Porous Materials
In the dynamic world of digital printing, UV flatbed printers have emerged as a game-changer, enabling businesses to produce high-quality prints on a vast array of surfaces. One of the most intriguing applications of these printers is their ability to print on porous materials—substances that absorb ink rather than repel it. From textured fabrics to unfinished wood and natural stone, porous materials add a unique aesthetic to printed products but also present unique challenges. This article explores practical tips and techniques to achieve stunning results when using UV flatbed printers on porous surfaces, ensuring vibrant colors, sharp details, and long-lasting durability.
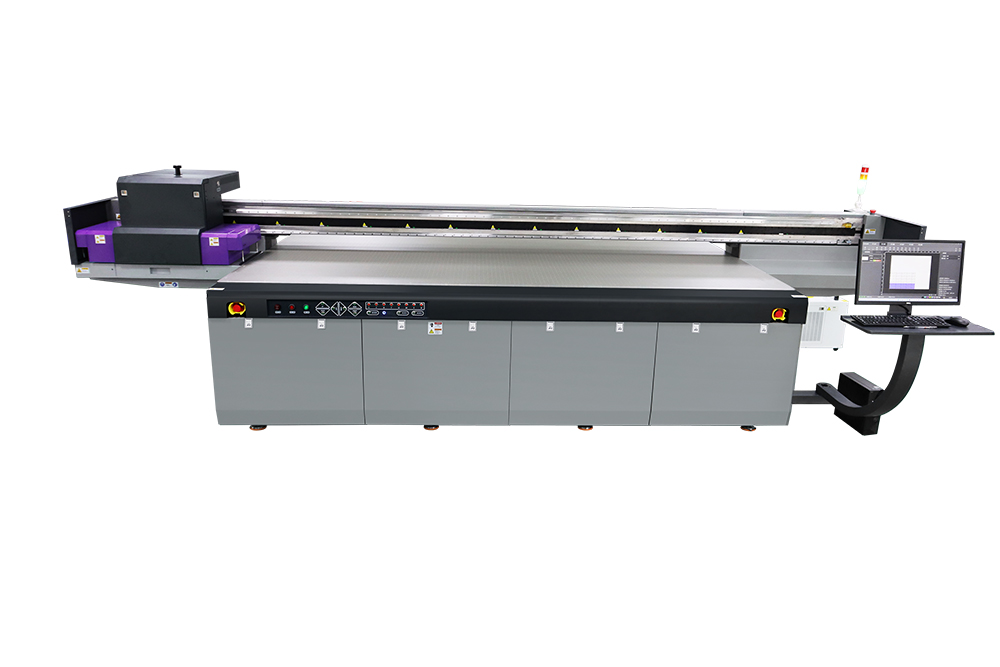
Understanding Porous Materials and Their Challenges
Porous materials, such as untreated wood, canvas, cork, and certain types of stone, contain tiny pores or voids that allow liquids like ink to penetrate their surface. While this absorption can create beautiful, matte finishes, it also poses risks. If not managed correctly, ink can bleed, blurring fine details and diluting color intensity. Additionally, uneven absorption across the material’s surface can lead to inconsistent print quality.
UV-curable inks, commonly used in flatbed printers, harden instantly when exposed to ultraviolet light. However, their rapid curing doesn’t eliminate the need for proper preparation. Without pre-treatment or optimized settings, prints on porous materials may fade prematurely, scratch easily, or fail to adhere correctly. Understanding these challenges is the first step toward mastering printing on porous surfaces.
Preparing the Material: The Foundation of Success
The key to a flawless print on porous surfaces lies in thorough preparation. Begin by cleaning the material to remove dust, debris, or oils that could interfere with ink adhesion. Use a lint-free cloth or compressed air for delicate items like textiles, and a damp cloth for wood or stone. Ensure the surface is completely dry before printing.
For highly absorbent materials, applying a primer or pre-treatment coat is often necessary. This step fills the pores slightly, creating a smoother surface for the ink to rest upon while still allowing some absorption for a natural finish. Choose a pre-treatment designed for your specific material and follow the manufacturer’s instructions for application. Some printers may recommend light sanding for wood or stone to enhance adhesion.
Finally, secure the material firmly to the printer’s bed using a vacuum system or adhesive tape to prevent shifting during printing. Uneven movement could distort the design, especially on textured surfaces.
Optimizing Printer Settings for Porous Surfaces
Modern UV flatbed printers offer customizable settings to accommodate various materials. For porous substrates, adjust the following parameters:
Ink Drop Size and Density: Increase ink drop size slightly to compensate for absorption. However, avoid over-saturation, which can cause bleeding. Balance density settings to ensure full coverage without pooling.
Curing Time and Intensity: UV lamps must cure the ink thoroughly before it has a chance to soak too deeply into the material. Test different curing speeds and lamp intensities to find the sweet spot where the ink hardens quickly but doesn’t crack due to rapid shrinkage.
Print Height and Z-Axis Adjustment: Porous materials often have uneven surfaces. Use the printer’s height-sensing technology to map the material’s topography and adjust the print head’s distance accordingly. This prevents smudging on raised areas and ensures even ink deposition.
White Ink Layer (If Applicable): For dark or translucent porous materials, applying a white ink base layer enhances color vibrancy. Adjust the opacity and thickness of this layer to block the underlying material’s hue without obscuring texture.
Mastering Color Management on Porous Substrates
Achieving accurate, vivid colors on porous materials requires careful color calibration. Porous surfaces inherently absorb more ink, which can dull hues compared to non-porous materials like glass or metal. To combat this:
Use a Color Profiling Tool: Create custom ICC profiles for each porous material you work with. These profiles adjust color values to compensate for absorption, ensuring what you see on-screen matches the final print.
Adjust Saturation and Brightness: In your design software, slightly boost saturation and brightness levels before printing. This counteracts the muting effect of absorption. However, avoid overcompensation, which could lead to garish colors.
Test Prints Are Essential: Always run test prints on scrap material before finalizing a job. Evaluate color accuracy, contrast, and detail sharpness. Make incremental adjustments until you’re satisfied with the results.
Post-Printing Care: Sealing and Finishing
Even with optimized printing, porous materials may benefit from post-processing to enhance durability and appearance. Sealants or varnishes designed for UV-printed surfaces create a protective barrier, preventing ink from wearing off or fading due to UV exposure, moisture, or abrasion.
Choose a sealant compatible with your material and ink type. Matte finishes preserve the natural texture of porous surfaces, while glossy options add depth and vibrancy. Apply the sealant evenly using a spray or brush, following the manufacturer’s drying time recommendations.
For textiles, consider heat-setting the print if the material and ink allow it. This process bonds the ink more firmly to the fibers, improving washability and longevity.
Troubleshooting Common Issues
Despite meticulous preparation, issues may arise. Here’s how to address them:
Bleeding or Blurring: If ink spreads beyond the design, reduce ink density or increase curing time. For highly absorbent materials, apply a thicker pre-treatment layer.
Uneven Curing: Patches of uncured ink indicate insufficient UV exposure. Adjust lamp intensity or slow the print head’s speed. Ensure the material isn’t blocking UV light from reaching certain areas.
Adhesion Problems: If the print flakes or peels, the material may need a stronger pre-treatment or primer. Alternatively, the ink may not be compatible with the substrate—test alternative ink formulations if possible.
Texture Interference: On very rough surfaces, ink may not reach recessed areas. Lightly sand the material to smooth it or opt for a design with larger, simpler elements.
Embracing Creativity: Unique Applications for Porous Materials
The ability to print on porous materials opens doors to innovative applications. Consider these ideas:
Custom Furniture and Home Decor: Print intricate patterns or artwork onto wooden tables, headboards, or decorative tiles for a personalized touch.
Eco-Friendly Packaging: Use porous, biodegradable materials like recycled cardboard or bamboo for sustainable packaging with branded designs.
Textile Innovations: From canvas tote bags to upholstery fabric, printing on porous textiles allows for soft, breathable products with high-resolution graphics.
Artistic Installations: Artists can leverage porous stones, ceramics, or even concrete to create large-scale murals or sculptures with UV-printed details.
Conclusion
Printing on porous materials with a UV flatbed printer requires patience, experimentation, and attention to detail. By understanding the material’s properties, optimizing printer settings, and mastering color management, businesses can unlock stunning results that blend creativity with technical precision. Whether you’re producing bespoke home decor, eco-conscious packaging, or artistic masterpieces, porous substrates offer a canvas like no other. With the tips outlined in this guide, you’re well-equipped to tackle these challenges and elevate your printing projects to new heights.