UV Flatbed Printer: Tips for Printing on Delicate Materials
In today’s dynamic printing industry, UV flatbed printers have revolutionized how businesses approach customization and large-format production. Their ability to print directly onto rigid and flexible substrates—including delicate materials like textiles, thin plastics, leather, and specialty papers—has opened doors for creative applications. However, printing on fragile surfaces requires precision, patience, and the right techniques to avoid damage, ink smudging, or uneven coverage. This article explores actionable tips for achieving flawless results on delicate materials using UV flatbed printers, ensuring both quality and material integrity.
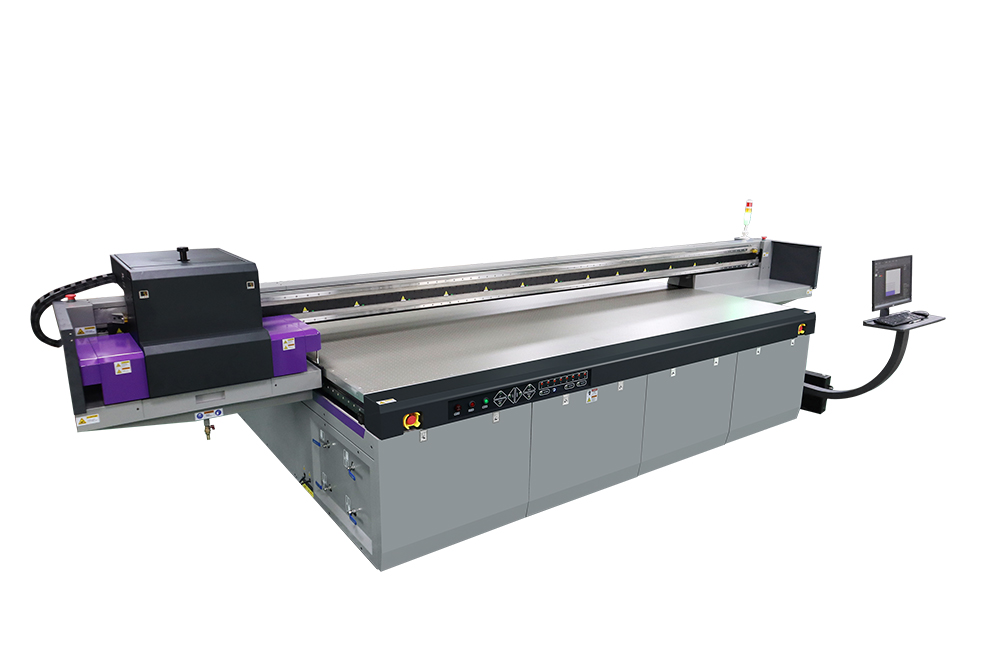
Understanding Delicate Materials: Key Challenges
Delicate materials often share common vulnerabilities that complicate the printing process. Thin textiles may warp under pressure, while coated papers or vinyl can crack if handled roughly. Even the chemical composition of some substrates—like water-resistant synthetic fabrics—might resist ink adhesion. UV printers, which cure ink instantly with UV light, offer advantages such as quick drying times and vibrant colors. However, their mechanical and thermal demands (e.g., printhead height, UV exposure) must be calibrated to suit fragile surfaces.
Common Risks:
Material Distortion: Excessive pressure from the print bed or vacuum system can stretch or dent thin materials.
Ink Cracking: Rapid curing on flexible substrates may cause ink layers to fracture when bent.
Adhesion Issues: Smooth or non-porous surfaces might reject ink, leading to peeling or fading.
To mitigate these risks, operators must tailor their approach to each material’s unique properties.
Preparing Your Workspace and Materials
A successful print job begins long before the printer starts running. Start by creating a controlled environment to minimize variables that could affect delicate materials.
Climate Control: Maintain a stable room temperature (ideally 68–77°F or 20–25°C) and humidity level (40–60%). Sudden temperature swings or dry air can cause materials like thin papers to curl or static electricity to build up, disrupting alignment.
Static Elimination: Use anti-static mats or sprays to prevent materials from clinging to the print bed or attracting dust. Static charges are particularly problematic for lightweight fabrics and synthetic films.
Surface Cleaning: Gently wipe substrates with a microfiber cloth or compressed air to remove debris. Avoid solvents that could dissolve coatings or weaken the material.
Material Mounting: Secure delicate items to the print bed using low-tack adhesive mats or vacuum systems with adjustable suction. For ultra-thin materials, consider sandwiching them between carrier sheets to add rigidity.
Optimizing Printer Settings for Fragile Substrates
UV flatbed printers offer adjustable parameters that directly impact print quality on delicate materials. Here’s how to fine-tune them:
Printhead Height: Raise the printhead slightly to reduce pressure on fragile surfaces. Most printers allow manual adjustments in 0.1mm increments. Test with a sacrificial sheet first to avoid scratches.
Ink Drop Size: Use smaller drop sizes (e.g., 5–10 picoliters) for detailed prints on thin materials. Larger drops may pool or bleed on non-absorbent surfaces.
Curing Intensity: Lower UV lamp power or increase the printhead’s travel speed to prevent overheating. Delicate materials like PVC film or heat-sensitive fabrics can warp under prolonged UV exposure.
Pass Count: Increase the number of print passes to build up ink density gradually. This reduces the risk of ink saturation while ensuring opacity.
Always conduct test prints on scrap material before committing to a full job. Document successful settings for future reference.
Choosing the Right Ink and Curing Strategy
Not all UV inks are created equal, especially for delicate substrates. Here’s what to consider:
Flexible vs. Rigid Inks: Opt for flexible ink formulations when printing on stretchable or bendable materials (e.g., vinyl banners, leather goods). Rigid inks, while durable, may crack when the substrate flexes.
Adhesion Promoters: Apply a thin layer of primer or adhesion promoter to glossy or non-porous surfaces. Let it dry completely before printing to improve ink bonding.
Curing Timing: Avoid “over-curing” by monitoring the distance between the printhead and UV lamps. Some printers offer “delay” settings to allow ink to level before full curing, reducing surface roughness.
Post-Curing Care: Let prints cool for 10–15 minutes after curing to prevent heat-induced shrinkage. For heat-sensitive materials, consider air-drying for a few hours before final curing.
Handling and Post-Processing Delicate Prints
The job isn’t done once the printer stops. Proper post-processing ensures longevity and prevents damage.
Gentle Removal: Use a plastic spatula or your fingers (wearing gloves) to lift prints from the bed. Avoid metal tools that could gouge soft materials.
Cooling Period: Allow prints to rest in a flat, dust-free area for at least 30 minutes before trimming or assembling. This reduces the risk of ink cracking during cutting.
Finishing Touches: Apply a clear protective coating for added durability, especially on outdoor-facing prints. Use a soft brush or spray to avoid abrading the surface.
Storage: Roll textiles or large prints around a sturdy tube to prevent creasing. Store flat items between acid-free tissue paper.
Troubleshooting Common Issues
Even with careful planning, problems can arise. Here’s how to fix them:
Ink Smudging: If ink rubs off, the material may be too smooth or the curing insufficient. Try:
Increasing UV lamp intensity or slowing print speed.
Adding a textured primer layer.
Material Warping: If the substrate curls or bends, reduce printhead pressure or lower the bed temperature.
Color Inconsistency: Uneven curing (e.g., shadows from uneven lamp placement) can cause streaks. Regularly clean UV lamps and recalibrate the printer.
Static Buildup: If prints attract dust mid-process, ground your workspace and use ionizing fans.
Expanding Your Capabilities: Advanced Techniques
Once you’ve mastered the basics, experiment with creative applications:
Layered Prints: Print a base layer, cure it partially, then add a second layer for depth. Works well on textured fabrics.
Embossed Effects: Use a clear gloss ink to create raised textures by adjusting curing timing.
Hybrid Printing: Combine UV printing with heat transfers or foil stamping for multi-media projects.
Final Thoughts
Printing on delicate materials with a UV flatbed printer is a blend of art and science. By understanding material behavior, optimizing printer settings, and refining post-processing techniques, businesses can unlock new revenue streams in fashion, interior design, packaging, and beyond. The key? Start small, test relentlessly, and embrace experimentation. With patience, even the most fragile substrates can become canvases for stunning, durable prints.