UV Flatbed Printer: Tips for Achieving Consistent Registration and Alignment
In the realm of digital printing, UV flatbed printers have revolutionized the way we approach printing on a variety of substrates, from rigid materials like glass and metal to flexible ones like vinyl and fabric. The versatility and precision of these machines make them a staple in the printing industry, especially for those seeking to produce high-quality graphics with intricate details and vibrant colors. However, one of the most critical aspects of operating a UV flatbed printer efficiently is achieving consistent registration and alignment. Without it, even the most beautifully designed prints can suffer from misalignment, overlapping, or gaps, drastically reducing their visual appeal and professional quality.
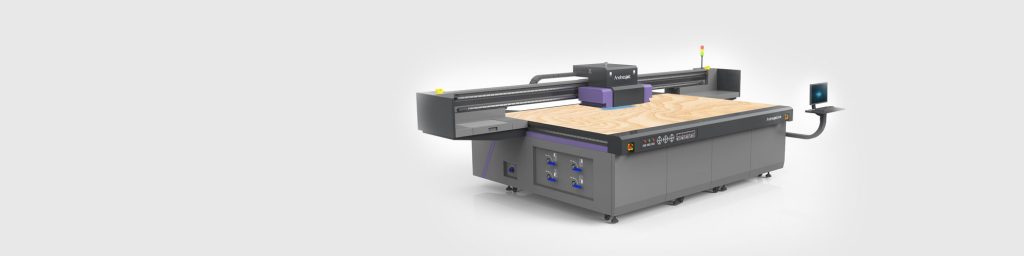
Achieving and maintaining consistent registration and alignment is not a task for the faint-hearted; it requires a keen understanding of your printer’s capabilities, meticulous preparation, and ongoing adjustments. In this article, we will delve into the intricacies of registration and alignment in UV flatbed printing, offering practical tips and strategies to help you master this essential aspect of the process.
Understanding Registration and Alignment
Before we dive into the tips, it’s crucial to understand what registration and alignment mean in the context of UV flatbed printing. Registration refers to the accuracy of the printed image’s position relative to the substrate and to any other printed elements. Alignment, on the other hand,pertains to the precision of the image’s placement across multiple passes or printheads. Both are vital for ensuring that the final print is cohesive, with all elements fitting together perfectly.
1. Prepare Your Substrate Properly
The first step towards achieving consistent registration and alignment begins with substrate preparation. Ensure that the surface is clean, dry, and free of any contaminants that could interfere with the printing process. Dust, oils, and moisture can all cause the substrate to shift slightly during printing, leading to misalignment. Additionally, make sure the substrate is securely fastened to the printer’s bed to prevent any movement during printing. Using adhesive sprays or tapes designed for UV printing can help achieve this.
2. Calibrate Your Printer Regularly
Calibration is the backbone of consistent registration and alignment. It involves adjusting the printer’s settings to ensure that the printheads are aligned correctly and that the printer’s internal measurements match the actual dimensions of the substrate. Most UV flatbed printers come with built-in calibration tools and procedures. Perform these calibrations regularly, especially after any major maintenance or when switching between different substrate types or thicknesses.
3. Use High-Quality Print Files
The quality of your print files can significantly impact registration and alignment. Ensure that your design files are created at the correct resolution (typically 300 dpi for high-quality prints) and that they are saved in a format compatible with your printer’s RIP software. Avoid using low-resolution images or files with compressed image data, as these can lead to pixelation and registration issues. Additionally, make sure that all elements in your design are properly aligned and that there are no hidden layers or objects that could cause unexpected printing artifacts.
4. Optimize Your Print Settings
The print settings you choose can also affect registration and alignment. Start by selecting the appropriate print mode for your job. For instance, if you’re printing on a rigid substrate, use a setting that accommodates the material’s stiffness and weight. Adjust parameters such as print speed, ink drop size, and pass count to ensure optimal ink deposition and minimize the risk of misalignment. Remember, slower print speeds and multiple passes can often yield better registration at the expense of productivity.
5. Control Environmental Factors
Environmental conditions can play a significant role in the printing process. Temperature and humidity fluctuations can cause the substrate to expand or contract slightly, leading to registration issues. Maintain a stable environment in your printing area, ideally with a temperature of around 20-25°C and a relative humidity of 40-60%. Using a dehumidifier or humidifier can help regulate these conditions, ensuring more consistent print results.
6. Employ Registration Marks
Many UV flatbed printers utilize registration marks to aid in the alignment process. These marks are printed along the edges of the substrate and are read by the printer’s sensors to ensure accurate placement of subsequent passes. Make sure these marks are clearly visible and not obscured by any part of your design. If your printer allows, consider using automatic registration adjustment features that rely on these marks to correct any minor misalignments during printing.
7. Monitor and Maintain Printheads
The condition of your printheads directly impacts registration and alignment. Regularly clean and maintain the printheads according to the manufacturer’s recommendations. Clogged or misaligned nozzles can cause ink to be deposited incorrectly, leading to misregistration. Perform nozzle checks and cleanings as needed, and replace any worn-out or damaged printheads promptly.
8. Utilize Print Preview and Test Prints
Before committing to a full print job, use the printer’s print preview function to simulate the printing process. This can help identify potential registration issues before they occur. Additionally, perform test prints on a scrap piece of the same substrate to ensure that everything is aligned correctly. Pay close attention to registration marks and the alignment of multi-color prints during these tests.
9. Adjust for Material Shrinkage or Expansion
Certain substrates, especially those made from plastics or fabrics, may shrink or expand slightly when exposed to UV inks or the heat generated during the printing process. Be aware of these material characteristics and adjust your print settings accordingly. If possible, pre-treat the substrate to minimize these effects or allow it to acclimate to the printing environment before printing.
10. Train Your Operators
Finally, consistent registration and alignment also depend on the skill and knowledge of the printer operators. Provide comprehensive training to your team on the proper use and maintenance of the UV flatbed printer. Emphasize the importance of following established procedures and encourage them to report any issues or anomalies they encounter during the printing process.
Achieving consistent registration and alignment in UV flatbed printing is a multifaceted challenge that requires attention to detail, regular maintenance, and a thorough understanding of both your printer and the materials you’re working with. By following the tips outlined above, you can significantly improve the quality and consistency of your prints, ensuring that each job meets the high standards your customers expect. Remember, the key to success lies in meticulous preparation, ongoing adjustments, and a commitment to continuous learning and improvement. With these practices in place, you’ll be well-equipped to tackle even the most complex printing projects with confidence and precision.