UV Flatbed Printer: The Role of Print Bed Coating
UV flatbed printers have revolutionized industries ranging from advertising and signage to packaging and custom manufacturing. Their ability to print directly onto rigid substrates—such as acrylic, wood, metal, and glass—with vibrant colors and intricate details has made them indispensable tools for businesses seeking efficiency and creativity. Yet, beneath the high-tech mechanics of inkjet nozzles and UV curing lamps lies a critical component often overlooked: the print bed coating. This layer, applied to the printer’s surface, serves as the foundation for every print job, influencing adhesion, durability, and overall print quality. In this blog, we explore the multifaceted role of print bed coatings in UV flatbed printing, their composition, and why they matter for businesses aiming to maximize output and minimize waste.
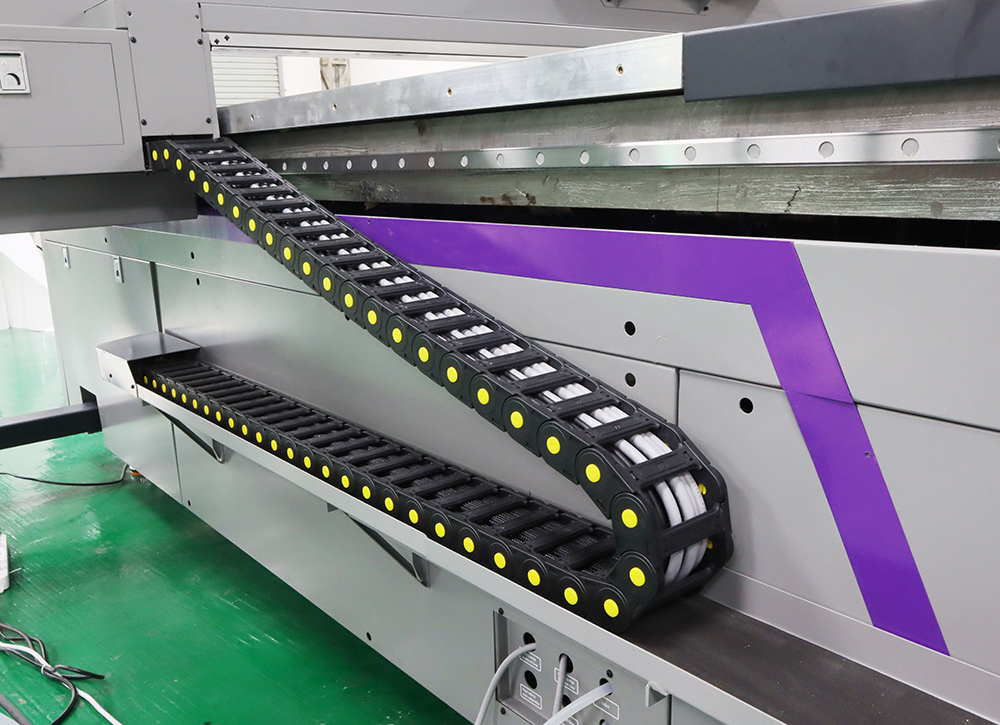
1. Enhancing Substrate Adhesion: The Science of Sticking
The primary function of a print bed coating is to create a bond between the substrate and the UV-curable ink. Unlike traditional solvent-based inks, which rely on evaporation to dry, UV inks cure instantly when exposed to ultraviolet light. However, this rapid curing process demands a surface that ensures proper ink adhesion. Without the right coating, inks may fail to adhere to smooth or non-porous materials like glass or metal, resulting in smudging, peeling, or uneven prints.
Print bed coatings are formulated with chemical properties tailored to specific substrates. For example, a coating designed for acrylic might include polymers that improve ink absorption, while a metal-focused formula could feature primers that etch the surface microscopically. By customizing the coating, printers ensure consistent adhesion, reducing the risk of costly reprints and material waste.
2. Preventing Ink Bleeding and Ghosting: Achieving Crisp Edges
One of the most common challenges in UV flatbed printing is ink bleeding—where ink spreads beyond the intended design, blurring edges and degrading image clarity. This issue is particularly prevalent on porous substrates like untreated wood or certain plastics, which absorb ink unevenly. A high-quality print bed coating acts as a barrier, regulating ink absorption and ensuring precise placement.
Another related problem is “ghosting,” where residual ink from previous prints transfers onto subsequent jobs. Coatings with anti-static or non-stick properties mitigate this risk by creating a surface that repels ink residue. This not only preserves print quality but also streamlines production by reducing the need for frequent bed cleaning.
3. Extending Substrate Compatibility: Opening New Creative Horizons
The versatility of UV flatbed printers hinges on their ability to work with diverse materials. However, not all substrates are created equal. Some, like ceramics or certain coated papers, require pre-treatment to accept UV inks. Print bed coatings eliminate the need for substrate-specific pre-processing, expanding the range of materials a printer can handle without additional setup time or costs.
For instance, a furniture manufacturer might use a UV flatbed printer to customize tabletops with intricate designs. Without a specialized coating, printing directly on laminate or veneer surfaces could lead to poor adhesion or uneven curing. A compatible coating bridges this gap, enabling seamless integration of UV printing into the production workflow.
4. Protecting the Print Bed: Reducing Wear and Maintenance
UV flatbed printers are investments, and protecting their components is essential for longevity. The print bed, in particular, is subjected to constant pressure, heat, and chemical exposure. Coatings act as a sacrificial layer, shielding the bed from scratches, ink stains, and UV degradation. This not only prolongs the printer’s lifespan but also reduces downtime associated with maintenance or repairs.
Additionally, some coatings offer anti-corrosive properties, which are invaluable when printing on metal substrates. By preventing oxidation or chemical reactions between the substrate and the bed, these coatings ensure consistent performance over time.
5. Improving Curing Efficiency: Saving Time and Energy
UV curing is a delicate balance of light intensity, exposure time, and ink formulation. A print bed coating can influence this process by optimizing the substrate’s interaction with UV light. For example, coatings with light-diffusing properties might distribute curing energy more evenly, reducing the risk of under-cured or over-cured spots.
Efficient curing also translates to faster production speeds. When inks adhere properly and cure uniformly, printers can operate at higher throughputs without sacrificing quality. This efficiency is a game-changer for businesses with tight deadlines or large-volume orders.
6. Environmental and Safety Considerations: A Greener Approach
As sustainability becomes a priority for consumers and businesses alike, print bed coatings offer eco-friendly benefits. Water-based or low-VOC (volatile organic compound) formulations reduce harmful emissions during application and printing. Additionally, by minimizing ink waste and reprints, coatings contribute to a more sustainable production cycle.
Furthermore, some coatings are designed to be recyclable or biodegradable, aligning with circular economy principles. For businesses aiming to meet environmental certifications or appeal to eco-conscious clients, choosing the right coating can be a strategic decision.
7. Choosing the Right Coating: Factors to Consider
Selecting a print bed coating isn’t a one-size-fits-all decision. Key factors to evaluate include:
Substrate Type: Coatings vary in compatibility with materials like glass, metal, or textured plastics.
Application Method: Some coatings are spray-applied, while others are brushed or rolled on.
Drying Time: Faster-drying formulas reduce setup time but may require precise handling.
Cost vs. Performance: High-end coatings may offer superior durability but at a higher price point.
Printers should also consider partnering with coating suppliers who provide technical support and custom formulations. A tailored solution can address niche challenges, such as printing on curved surfaces or heat-sensitive materials.
Conclusion: The Unsung Hero of UV Flatbed Printing
In the world of UV flatbed printing, where innovation often focuses on ink technology or printhead precision, the print bed coating remains a quiet but critical component. From ensuring adhesion and preventing defects to extending equipment life and supporting sustainability, coatings are the unsung heroes of high-quality, efficient printing.
For businesses investing in UV flatbed technology, understanding the role of print bed coatings is essential. By choosing the right formulation and maintaining it properly, printers can unlock the full potential of their equipment, delivering results that meet—and exceed—client expectations. Whether you’re a small sign shop or a global manufacturing powerhouse, the right coating is the foundation upon which brilliance is built.