UV Flatbed Printer: The Impact of Temperature on Print Quality
The realm of digital printing has witnessed a remarkable evolution, with UV flatbed printers emerging as a cornerstone technology for industries ranging from advertising and signage to manufacturing and decorative arts. These printers are celebrated for their versatility, enabling high-resolution prints on a diverse array of substrates, including glass, metal, wood, and plastics. Yet, beneath their sleek exteriors lies a nuanced ecosystem where environmental factors, particularly temperature, play a pivotal role in determining the quality and consistency of the final output. This blog post delves into the intricate relationship between temperature and print quality, offering insights into how operators can optimize conditions to achieve exceptional results.
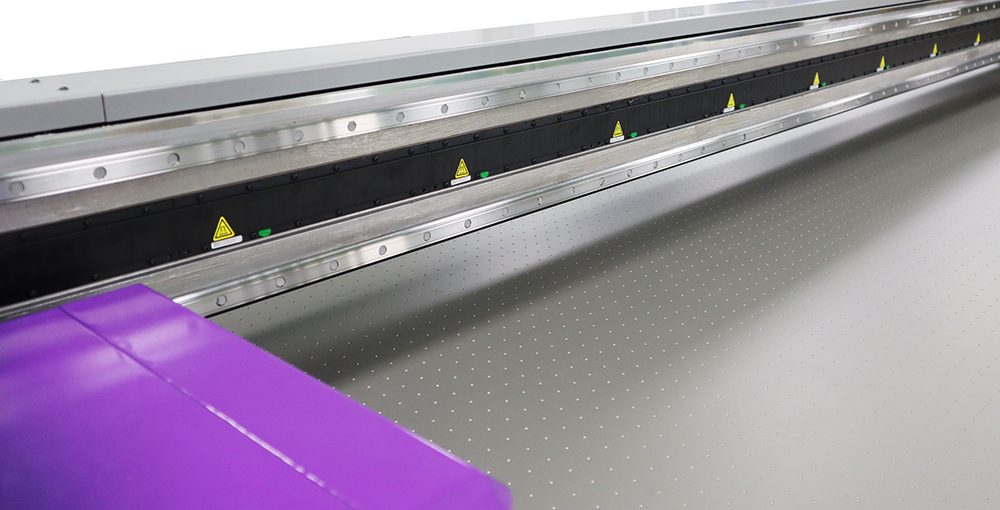
The Science of UV Curing and Temperature Sensitivity
At the heart of UV flatbed printing lies the UV curing process, a chemical reaction triggered by ultraviolet light that solidifies ink droplets instantly upon contact with the substrate. This rapid drying mechanism not only enhances production speed but also ensures the durability and vibrancy of prints. However, the efficiency of UV curing is highly dependent on ambient temperature. Extreme temperatures, whether too hot or too cold, can disrupt the chemical balance, leading to issues such as incomplete curing, adhesion problems, or ink cracking. For instance, in colder environments, the viscosity of the ink may increase, making it difficult for the printer to lay down precise droplets. Conversely, high temperatures can accelerate evaporation, causing the ink to dry prematurely within the print head, leading to clogs and inconsistent prints.
Ideal Temperature Ranges for Optimal Performance
Maintaining an optimal temperature range is crucial for ensuring the printer operates at peak efficiency. While specific requirements may vary depending on the model and ink formulation, a general guideline suggests keeping the print environment between 68°F (20°C) and 77°F (25°C). This range facilitates smooth ink flow, consistent droplet formation, and efficient UV curing. Operators should invest in reliable thermostats and HVAC systems to stabilize room temperature, especially in regions with extreme climates. Additionally, incorporating temperature sensors within the printer itself can provide real-time data, allowing for proactive adjustments to maintain optimal conditions.
Humidity: The Silent Partner in Temperature Management
While temperature often takes center stage, humidity is an equally critical factor in print quality. High humidity levels can increase ink viscosity and slow down drying times, potentially leading to smudging or ink bleeding. On the other hand, low humidity can cause the ink to dry too quickly, resulting in poor adhesion and cracking. Ideally, humidity should be maintained between 40% and 60% to complement the recommended temperature range. Dehumidifiers and humidifiers can be employed to regulate moisture levels, ensuring a balanced environment that supports both ink stability and UV curing efficiency.
Material Preparation and Temperature Considerations
The substrate itself is not immune to temperature’s influence. Materials such as plastics and metals can expand or contract with temperature fluctuations, affecting print registration and alignment. Preheating substrates to a consistent temperature before printing can mitigate these issues, ensuring that the material remains stable throughout the process. Moreover, some materials may require specific temperature settings to enhance ink adhesion. For example, printing on glass often necessitates a slightly higher temperature to improve the ink’s ability to bond with the smooth surface. Operators should consult material specifications and conduct test prints to determine the optimal conditions for each substrate.
Calibration and Maintenance: Key to Temperature Consistency
Regular calibration and maintenance are essential for maintaining print quality, especially in environments where temperature is a variable. Printers should be calibrated at the start of each shift or whenever there are significant temperature changes. This includes adjusting print head heights, nozzle alignments, and UV lamp intensities to compensate for any thermal expansion or contraction. Additionally, routine cleaning of print heads and UV lamps is crucial to prevent clogs and ensure consistent curing. By integrating these practices into a preventive maintenance schedule, operators can minimize downtime and extend the lifespan of their equipment.
Operator Training and Environmental Awareness
The human element plays a vital role in managing temperature-related challenges. Operators should be trained to recognize the signs of temperature-induced print defects, such as banding, streaking, or poor adhesion. They should also be equipped with the knowledge to troubleshoot common issues, such as adjusting print parameters or recalibrating the printer in response to temperature fluctuations. Furthermore, fostering an environmental awareness culture within the workplace encourages proactive measures, such as closing doors to prevent drafts or using thermal curtains to insulate the print area.
Conclusion
In the fast-paced world of digital printing, where every detail counts, understanding the impact of temperature on print quality is paramount. By embracing a holistic approach that considers temperature, humidity, material preparation, calibration, and operator training, businesses can unlock the full potential of UV flatbed printers, delivering vibrant, durable prints that exceed client expectations. As technology continues to advance, the marriage of precision engineering and environmental intelligence will remain at the forefront of driving innovation in the printing industry. So, the next time you marvel at a stunning UV-printed masterpiece, remember the invisible hand of temperature that made it all possible.