UV Flatbed Printer: The Impact of Ink Viscosity on Print Quality
UV flatbed printers have revolutionized the printing industry with their versatility, allowing businesses to produce high-quality graphics on diverse materials, from rigid substrates like glass and metal to flexible media like fabric and vinyl. Central to achieving consistent, vibrant prints is the ink viscosity—a property often overlooked but critical to performance. This article explores how ink viscosity influences print quality, the science behind it, and practical strategies for optimizing outcomes. By understanding this dynamic, users can unlock the full potential of their UV flatbed printers while avoiding common pitfalls.
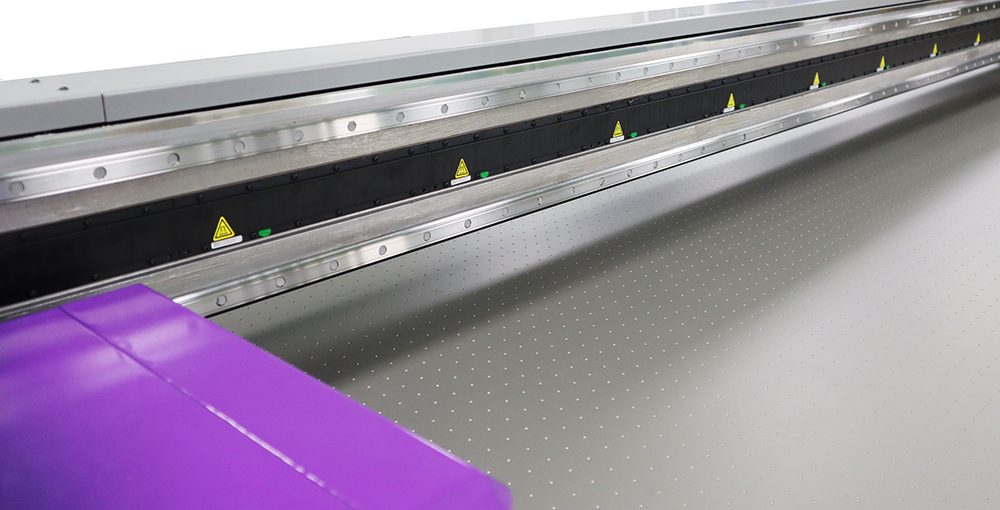
The Science Behind Ink Viscosity
Viscosity refers to a fluid’s resistance to flow. In UV flatbed printing, ink viscosity determines how easily the ink passes through the printer’s nozzles, adheres to substrates, and cures under UV light. Ideal viscosity ensures smooth ink transfer, precise dot placement, and uniform curing. However, deviations from the optimal range can lead to issues like nozzle clogs, uneven color distribution, or incomplete curing.
Several factors affect ink viscosity, including temperature, storage conditions, and formulation. For instance, cold environments may thicken inks, while prolonged exposure to heat can thin them. Printers must monitor these variables to maintain consistency. Additionally, UV inks are formulated with photoinitiators, monomers, and pigments that interact dynamically—making viscosity a delicate balance between stability and printability.
How Viscosity Affects Print Resolution and Detail
Print resolution hinges on the ink’s ability to form precise dots. If viscosity is too high, ink may struggle to exit nozzles, resulting in jagged edges, satellite drops (secondary ink splatters), or gaps in the print. Conversely, low-viscosity ink can cause overspray, bleeding, or feathering, blurring fine details. High-resolution prints, such as photographic reproductions or intricate designs, demand strict viscosity control to preserve sharpness and clarity.
For example, a print shop producing custom wall art might notice pixelated edges or faded colors if the ink is too thick. Adjusting viscosity—typically by warming the ink or modifying the formulation—can restore crispness. Modern UV flatbed printers often include viscosity sensors and automated adjustments to mitigate these risks, but manual calibration remains essential for niche applications.
The Role of Viscosity in Color Consistency
Color accuracy is paramount in branding, packaging, and fine art reproduction. Viscosity fluctuations disrupt color consistency by altering ink flow rates across different nozzles. Over time, this inconsistency can lead to streaking, banding, or mismatched hues in multi-color prints. For instance, a business printing promotional banners might observe uneven reds or blues if the cyan ink’s viscosity varies between batches.
To combat this, operators must standardize ink handling protocols. Storing inks at controlled temperatures (usually 20–25°C or 68–77°F) and using stirrers to maintain homogeneity are proven strategies. Some printers also employ closed-loop systems that continuously monitor viscosity and adjust pressure or temperature in real time, ensuring color fidelity even during extended runs.
Curing Efficiency and Ink Adhesion: A Viscosity Balance
UV curing relies on photoinitiators reacting with UV light to solidify ink. However, viscosity directly impacts this process. Thick inks may cure unevenly, leaving tacky surfaces or weak adhesion, while overly thin inks could penetrate porous substrates too deeply, reducing vibrancy. For example, printing on uncoated wood might require slightly thicker ink to form a durable, glossy finish without sinking into the grain.
Substrate compatibility further complicates this equation. Smooth surfaces like acrylic demand lower-viscosity inks for even spreading, while textured materials like brick or canvas may benefit from thicker formulations to fill crevices. Testing viscosity levels for each material type ensures optimal curing and longevity of the final product.
Addressing Common Viscosity-Related Print Issues
Even with meticulous preparation, viscosity-related problems can arise. Common symptoms include:
Nozzle clogs: Thick ink or debris accumulation halts ink flow.
Orange peel texture: Uneven curing due to inconsistent ink layers.
Delamination: Poor adhesion causing layers to separate.
To resolve these, operators can:
Clean nozzles regularly using printer-approved solvents.
Filter inks to remove particulates that thicken the mixture.
Adjust printhead height to accommodate substrate textures.
Recalibrate viscosity settings based on environmental changes.
For instance, a signage company experiencing streaking on aluminum panels might resolve the issue by increasing the printhead’s distance from the surface, allowing thicker ink to settle evenly before curing.
Environmental and Operational Factors Influencing Viscosity
Ambient conditions play a significant role in ink viscosity. Humidity, temperature, and airflow near the printer can all cause fluctuations. In hot, dry climates, inks may evaporate rapidly, thickening between refills. Cold storage areas, on the other hand, can slow ink flow, leading to under-extrusion.
To mitigate these effects:
Install climate control systems in print shops to stabilize temperatures.
Use insulated ink containers during transport.
Schedule maintenance during off-peak hours to avoid temperature extremes.
Operators should also log environmental data alongside print jobs to identify patterns. For example, if morning prints consistently show streaking, it may indicate overnight cooling of the ink supply.
Conclusion: Mastering Viscosity for Superior Print Quality
UV flatbed printing’s success hinges on mastering ink viscosity—a nuanced yet critical aspect of the process. By understanding how viscosity impacts resolution, color, curing, and adhesion, printers can troubleshoot issues proactively and elevate their output. Implementing best practices like climate control, regular maintenance, and substrate-specific testing ensures consistent, high-quality results across applications.
As the industry evolves, advancements in ink chemistry and printer automation will likely simplify viscosity management. However, the fundamental principles remain unchanged: balance, precision, and adaptability are the keys to unlocking the full potential of UV flatbed technology. Whether producing intricate artworks or durable industrial labels, viscosity awareness sets apart average printers from those who deliver excellence.