UV Flatbed Printer: The Impact of Humidity on Print Quality
In the world of digital printing, UV flatbed printers have emerged as a game-changer, offering unparalleled versatility for businesses ranging from signage shops to custom furniture manufacturers. These machines use ultraviolet light to cure inks instantly, enabling vibrant colors, sharp details, and durability on diverse materials. Yet, achieving consistent print quality isn’t just about the printer’s technology—it’s also about understanding environmental factors. One of the most critical yet often overlooked variables? Humidity.
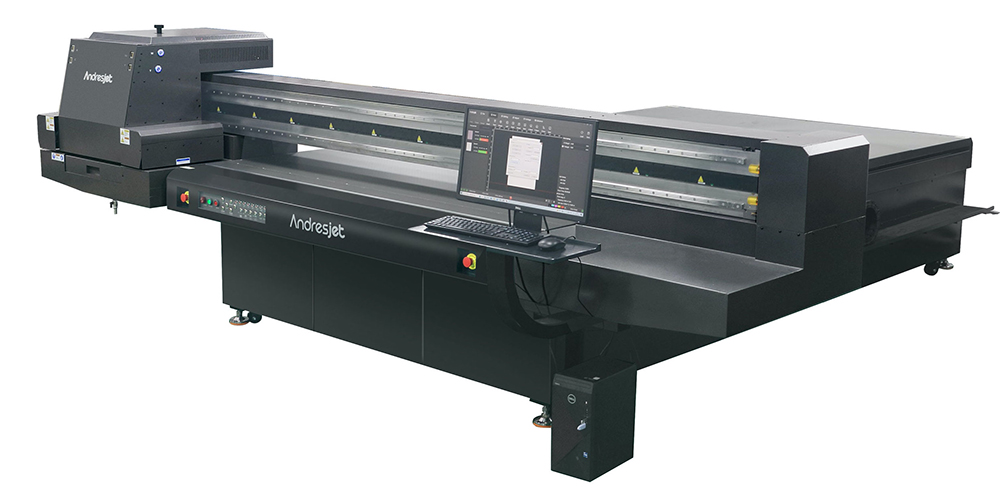
This article explores how humidity levels influence UV flatbed printing outcomes, offering actionable insights for operators to optimize their workflows. By delving into the science behind ink-material interactions, equipment maintenance, and storage practices, readers will discover how small adjustments in humidity control can lead to significant improvements in print quality, efficiency, and longevity.
The Science Behind Humidity and UV Ink Behavior
UV-curable inks are a marvel of modern chemistry, designed to transition from liquid to solid in seconds when exposed to UV light. However, their performance is highly sensitive to moisture in the air. High humidity introduces water vapor into the printing environment, which can disrupt the ink’s chemical balance.
When humidity levels rise above 60%, excess moisture can infiltrate ink droplets as they’re ejected from the printer’s printheads. This leads to uneven curing, where some areas of the ink remain tacky or fail to adhere properly to the substrate. Conversely, in overly dry conditions (below 30% humidity), inks may dry too quickly within the printhead nozzles, causing clogs and inconsistent droplet formation.
The result? Print defects like banding, color shifting, or poor adhesion—all of which waste materials and time. Understanding this delicate interplay between ink and humidity is the first step toward mastering print quality.
Substrate Sensitivity: How Materials React to Moisture
Not all printing materials respond to humidity in the same way. Porous substrates like wood, canvas, or uncoated papers absorb moisture from the air, swelling slightly before printing. This expansion can cause misalignment between color layers during multipass printing, resulting in blurry images or ghosting effects.
Non-porous materials like glass, metal, or acrylic don’t absorb moisture but can still be affected by static electricity, which builds up more readily in dry environments. Static charges attract airborne dust particles to the substrate’s surface, leading to pinholes or rough textures in the final print.
Operators must tailor their humidity control strategies based on the substrate. For example, printing on wood might require slightly lower humidity (40–50%) to minimize swelling, while acrylic sheets could benefit from a narrower range (45–55%) to reduce static.
Equipment Maintenance: Protecting Your Investment
UV flatbed printers are sophisticated machines, and their printheads are particularly vulnerable to humidity extremes. In humid conditions, condensation can form inside the printer, corroding internal components or shorting electrical connections. Over time, this shortens the equipment’s lifespan and increases repair costs.
To mitigate risks:
Install a dehumidifier in the printing area to keep humidity between 40% and 60%.
Use air filters to trap dust and moisture-laden particles before they reach the printer.
Schedule regular printhead cleanings to remove dried ink residue, which accumulates faster in dry air.
Store spare inks and substrates in climate-controlled cabinets to prevent premature curing or warping.
Proactive maintenance not only preserves print quality but also extends the printer’s operational life, saving businesses thousands of dollars in the long run.
Color Consistency: The Role of Environmental Stability
For businesses relying on precise color matching—such as packaging printers or fine art reproducers—humidity fluctuations are a silent enemy. Even a 10% swing in humidity can alter how ink droplets spread and dry on a substrate, leading to visible color shifts between print jobs.
To maintain color accuracy:
Calibrate the printer daily using a spectrophotometer to account for environmental changes.
Document humidity levels during each print run and correlate them with color profiles.
Use ICC profiles tailored to specific humidity ranges to ensure consistent output.
By treating humidity as a variable in the color management workflow, operators can deliver reliable results that meet clients’ expectations—every time.
Drying and Curing: Optimizing Post-Print Handling
After printing, humidity continues to impact the final product. In high-humidity environments, UV-cured inks may feel tacky for hours or even days, especially on porous substrates. This delay can disrupt production timelines if prints need to be laminated, cut, or assembled immediately.
To expedite drying:
Increase ventilation in the workspace to promote air circulation.
Use heated platforms under the printer to warm the substrate slightly, accelerating moisture evaporation.
Avoid stacking freshly printed materials until they’re fully cured to prevent smudging or blocking.
For businesses operating in consistently humid climates, investing in a dedicated curing chamber with controlled temperature and humidity settings can be a game-changer.
Best Practices for Humidity Control in Print Shops
Achieving ideal humidity levels doesn’t require a laboratory-grade environment. Here are practical steps any print shop can take:
Monitor humidity in real time using a digital hygrometer placed near the printer.
Adjust HVAC systems to maintain a stable range (40–60% RH is ideal for most applications).
Isolate the printer area from doors, windows, or areas prone to temperature swings.
Educate staff on the importance of humidity control and how to spot early signs of issues (e.g., streaky prints, nozzle clogs).
By making humidity management a standard operating procedure, teams can minimize waste, reduce reprints, and build a reputation for reliability.
Conclusion: Taking Charge of Your Print Environment
UV flatbed printing is a blend of art and science, and humidity control is the unsung hero of consistent quality. By understanding how moisture interacts with inks, substrates, and equipment, operators can transform their print shop into a precision-driven powerhouse.