UV Flatbed Printer: Printing on Foam and Rubber
In today’s dynamic world of visual communication, businesses and creatives are constantly seeking innovative ways to stand out. Traditional printing methods often fall short when it comes to non-porous, flexible, or textured materials like foam and rubber. Enter the UV flatbed printer—a game-changing technology that unlocks endless possibilities for printing on unconventional surfaces. This article explores how UV flatbed printers are revolutionizing industries by enabling high-quality, durable prints on foam boards, rubber mats, promotional items, and more.
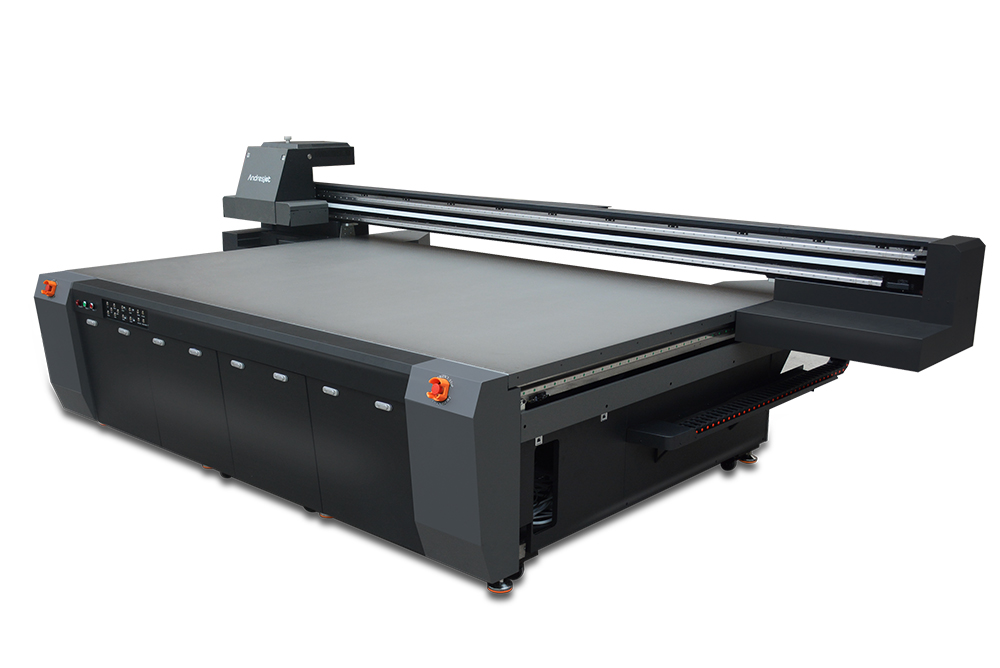
The Science Behind UV Flatbed Printing: How It Works
UV flatbed printers utilize ultraviolet light to cure inks instantly upon contact with the substrate. Unlike solvent-based inks that require time to dry or evaporate, UV inks harden under UV lamps, creating a bond that adheres firmly to the material. This process eliminates the need for pre-treatment or post-drying, streamlining production and reducing turnaround times.
For foam and rubber, this technology is particularly transformative. These materials often have uneven textures, porosity variations, or chemical compositions that challenge traditional printing methods. UV inks, however, are formulated to adapt to diverse surfaces, ensuring vibrant colors, sharp details, and long-lasting results.
Printing on Foam: From Signage to Custom Displays
Foam boards are a staple in advertising, exhibitions, and interior design due to their lightweight nature and versatility. Yet, achieving crisp graphics on foam without smudging or warping has historically been a hurdle. UV flatbed printers solve this by applying inks directly to the foam’s surface, which is then cured in seconds.
Advantages for Foam Applications:
Durability: UV-cured prints resist fading, scratches, and moisture, making them ideal for outdoor signage.
Texture Adaptability: Whether it’s smooth expanded polystyrene (EPS) foam or textured polyurethane (PU) foam, UV inks adhere uniformly.
Cost Efficiency: Direct-to-substrate printing eliminates the need for vinyl wraps or laminates, reducing material and labor costs.
Industries like retail, events, and architecture leverage UV printing on foam for 3D displays, trade show booths, and wall panels, combining aesthetics with practicality.
Rubber Printing: Turning Functional Items into Marketing Tools
Rubber, known for its flexibility and resilience, is ubiquitous in everyday life—from floor mats and coasters to industrial gaskets and promotional merchandise. However, printing on rubber demands inks that can withstand bending, stretching, and environmental exposure. UV flatbed printers rise to this challenge by delivering prints that flex without cracking or peeling.
Key Benefits for Rubber Substrates:
Flexibility: UV inks remain elastic after curing, ensuring prints on rubber retain their integrity even when stretched.
Weather Resistance: Outdoor rubber mats or automotive accessories printed with UV ink endure harsh UV rays, rain, and temperature fluctuations.
Customization Opportunities: Businesses can now personalize rubber items like yoga mats, bottle openers, or phone cases with intricate designs, turning functional objects into branding assets.
Overcoming Challenges: Adhesion and Material Preparation
While UV flatbed printers excel on foam and rubber, success hinges on proper material preparation.
Surface Cleaning: Dust, oils, or release agents on foam or rubber can hinder ink adhesion. A quick wipe with isopropyl alcohol or a dedicated cleaner ensures a pristine printing surface.
Priming for Porous Foams: Some foam types, like open-cell varieties, may benefit from a primer to seal pores and create a smoother base for ink.
Test Prints: Running sample prints on scrap material helps optimize settings for ink density, cure time, and print resolution.
By addressing these variables, users can achieve flawless results even on challenging substrates.
Industries Reaping the Benefits: Real-World Applications
UV flatbed printing on foam and rubber is reshaping multiple sectors:
Retail and Hospitality:
Custom-printed rubber floor mats with logos or safety messages enhance brand visibility in stores and restaurants.
Automotive and Manufacturing:
Durable rubber gaskets, seals, and panels are printed with part numbers, warnings, or branding for easy identification.
Sports and Recreation:
Foam exercise mats, yoga blocks, and protective gear showcase team logos or motivational graphics using UV printing.
Art and Design:
Artists create textured sculptures or wall art by printing vibrant designs on rigid foam boards, blending technology with creativity.
Events and Promotions:
Lightweight foam signs, step-and-repeat backdrops, and branded rubber coasters become memorable giveaways at trade shows or corporate events.
Environmental and Economic Perks: Sustainability Meets Efficiency
UV flatbed printers offer eco-friendly advantages compared to traditional methods:
Reduced Waste: Direct-to-substrate printing minimizes material use by eliminating the need for intermediate films or plates.
Low VOC Emissions: UV inks cure without releasing harmful volatile organic compounds (VOCs), making them safer for indoor environments.
Energy Efficiency: Instant curing under UV lamps consumes less power than heat-based drying systems.
Economically, businesses benefit from faster production cycles, reduced labor costs, and the ability to produce short-run custom orders profitably.
Future Trends: What’s Next for UV Printing on Flexible Substrates?
As technology evolves, UV flatbed printers are poised to push boundaries further:
Advanced Ink Formulations: New inks may offer enhanced flexibility, fire resistance, or anti-microbial properties for specialized applications.
Integration with AI and Automation: Smart printers could auto-detect material types and adjust settings, streamlining workflows for users.
3D and Textured Printing: Emerging techniques may allow raised or embossed effects on foam and rubber, adding tactile dimensions to designs.
Conclusion: The Future of Printing Is Unconventional
UV flatbed printers have shattered the limitations of traditional printing, empowering businesses to transform everyday items into canvases for creativity and branding. Whether it’s a durable rubber mat, a vibrant foam display, or a custom-designed promotional product, this technology delivers precision, speed, and sustainability.
For entrepreneurs, marketers, and manufacturers, embracing UV printing on foam and rubber opens doors to innovation, efficiency, and competitive advantage. As the industry continues to evolve, one thing is clear: the future of printing isn’t just flat—it’s flexible, textured, and full of potential.
Call to Action: Ready to explore UV printing for your next project? Reach out to a local print service provider or invest in a UV flatbed printer to unlock new revenue streams and creative possibilities. The world of unconventional surfaces awaits!