UV Flatbed Printer Ink Savings: Tips and Techniques
In the dynamic world of digital printing, UV flatbed printers have emerged as a game-changer for businesses seeking high-quality, durable prints on a variety of substrates. However, the cost of ink—a vital component of the printing process—can quickly escalate if not managed efficiently. For American businesses aiming to maximize profits while maintaining print quality, mastering ink-saving techniques is essential. This blog explores actionable tips and strategies to optimize ink usage without compromising output quality.
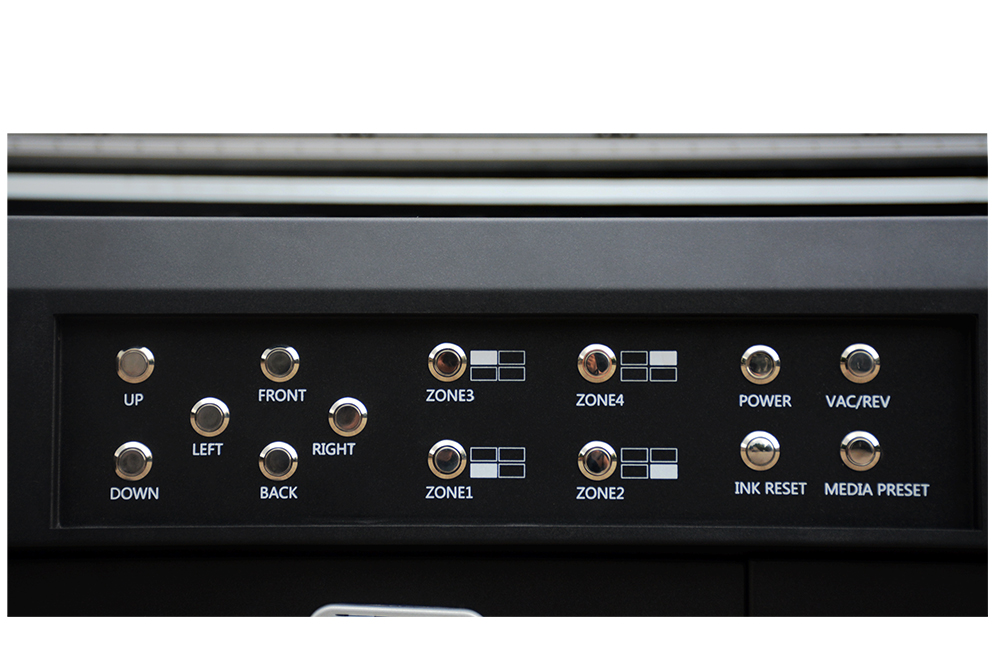
Understanding Ink Consumption in UV Flatbed Printing
Before diving into savings strategies, it’s crucial to grasp how ink is consumed. UV flatbed printers use ultraviolet light to cure ink instantly, allowing for printing on diverse materials like wood, glass, metal, and plastics. Ink usage depends on factors such as print resolution, substrate type, and image complexity. High-resolution prints or detailed graphics require more ink, while larger print areas naturally consume more resources. Recognizing these variables is the first step toward informed savings.
Optimize Print Settings for Cost Reduction
One of the most straightforward ways to reduce ink consumption is by adjusting print settings. Modern UV flatbed printers offer customizable options that can significantly impact ink usage. For instance, lowering the print resolution slightly (without sacrificing readability for non-critical applications) can lead to substantial ink savings. Similarly, enabling “draft mode” for internal use or proofs can minimize waste. Additionally, selecting the appropriate ink density—avoiding over-saturation—ensures optimal coverage without excess. Experiment with these settings on test prints to find the balance between quality and cost.
Proper Maintenance to Extend Ink Life
A well-maintained printer is more likely to use ink efficiently. Regular cleaning of print heads and nozzles prevents clogs that can lead to uneven ink distribution or wasted ink. Additionally, ensuring the printer’s calibration is accurate helps avoid over-inking in certain areas. Routine checks of ink levels and replacing cartridges or containers before they run dry can prevent emergencies that disrupt workflow and cause last-minute, high-cost ink replacements.
Strategic File Preparation for Ink Efficiency
The way a file is prepared before printing can influence ink usage. Simplifying designs by reducing unnecessary gradients, shadows, or overly complex patterns can lower ink demands. Using vector graphics instead of high-resolution images also reduces ink consumption, as vectors require less data to render. For text-heavy prints, choosing standard fonts over decorative ones can save ink while maintaining readability.
Substrate Selection: Matching Material to Ink Usage
Different substrates absorb ink differently, affecting how much is needed. Porous materials like fabric or uncoated paper tend to require less ink compared to non-porous surfaces like glass or metal. By understanding the substrate’s properties, printers can adjust settings or use specialized inks (where applicable) to optimize usage. For example, printing on glossy surfaces might necessitate higher ink volumes to achieve vibrant colors, whereas matte finishes could use less while still delivering quality results.
Advanced Techniques for Ink Optimization
Beyond basic settings, several advanced techniques can further reduce ink consumption:
Color Management: Using standardized color profiles (e.g., CMYK or Pantone systems) ensures consistent output with minimal ink waste.
Ink Layering: Adjusting the number of ink layers or using spot colors instead of full-color prints can lower costs.
White Ink Utilization: For dark substrates, using white ink as a base layer can enhance color vibrancy while potentially reducing the need for excessive CMYK ink.
Substrate Selection: Matching Material to Ink Usage
The choice of printing material directly impacts ink efficiency. Lightweight or porous substrates tend to absorb ink more readily, reducing the amount needed. Conversely, dense or non-porous materials might require more ink to achieve the same visual impact. By selecting substrates that align with print goals, businesses can optimize both cost and quality.
Monitoring and Continuous Improvement
Implementing a system to track ink usage—such as logging print jobs, analyzing data, and identifying trends—can reveal opportunities for further savings. For example, if certain files consistently use more ink than others, reviewing their design elements (e.g., gradients, solid colors) can guide future adjustments. Regularly reviewing ink consumption patterns also helps predict needs and avoid last-minute shortages.
Training and Skill Development
Equipping operators with the knowledge to optimize settings and troubleshoot common issues (e.g., nozzle clogs, ink viscosity adjustments) is vital. Well-trained staff can make real-time decisions to balance speed, quality, and cost.
Conclusion: Balancing Quality and Cost
In the competitive landscape of digital printing, mastering ink savings is a strategic advantage. By understanding ink consumption patterns, optimizing settings, and selecting appropriate substrates, businesses can reduce operational costs without compromising print quality. Remember, the goal is not merely to cut costs but to achieve a sustainable balance between efficiency and excellence. Embrace these tips, and watch your UV flatbed printing operations thrive—both economically and creatively.