UV Flatbed Printer: How to Adjust Print Settings for Best Results
UV Flatbed Printer: How to Adjust Print Settings for Best Results
UV flatbed printers have revolutionized the printing industry with their versatility and ability to print on a wide range of materials, including rigid substrates like metal, glass, wood, and plastics. These printers utilize UV-curable inks that are instantly dried by UV lights, resulting in high-quality, durable prints. However, achieving the best print results requires a keen understanding of the printer’s settings and some fine-tuning. In this comprehensive guide, we will delve into the critical aspects of adjusting the print settings on a UV flatbed printer to ensure optimal output.
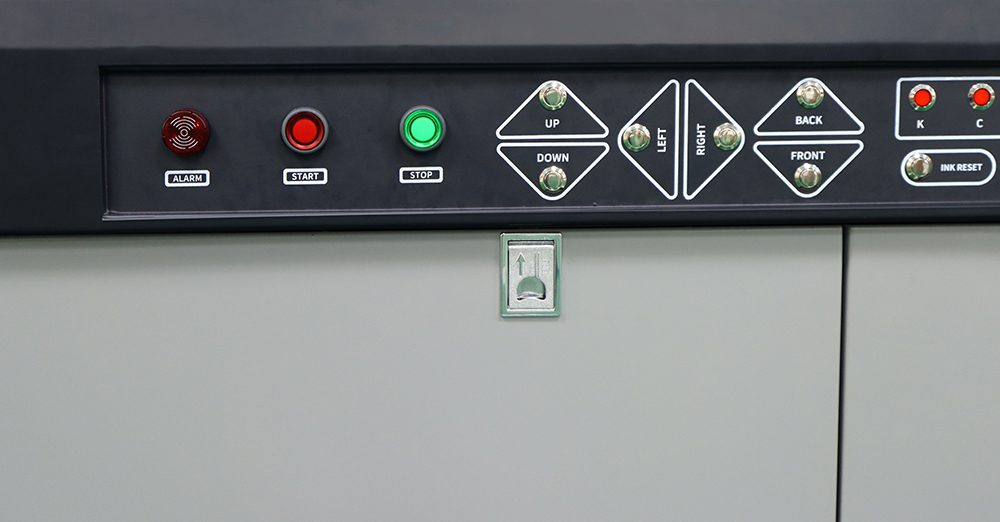
Understanding the Basics of UV Flatbed Printers
Before diving into the intricacies of print settings, it’s essential to grasp the fundamentals of UV flatbed printers. These machines are designed to print directly onto flat surfaces and can handle materials of various thicknesses and textures. The UV-curable inks used in these printers offer several advantages, such as:
Fast Curing: UV lights instantly cure the ink, which significantly reduces production time.
Enhanced Durability: The cured ink is resistant to fading, scratching, and water damage.
Vibrant Colors and Sharp Details: UV inks produce high-resolution prints with vivid colors and fine details.
Key Print Settings to Adjust
To achieve the best print quality, several settings need to be carefully adjusted. These include resolution, ink density, print speed, curing settings, and more. Let’s explore each of these in detail.
1. Resolution
Resolution refers to the number of dots per inch (DPI) in the print. Higher resolutions generally result in sharper and more detailed prints.
Standard Resolutions: Most UV flatbed printers offer resolutions ranging from 300 DPI to 2880 DPI.
Application-Specific Adjustments: For intricate designs requiring fine details, such as photographic images or fine art, opt for higher resolutions (1440 DPI or above). For more straightforward graphics or text, a lower resolution (300-600 DPI) may suffice.
2. Ink Density
Ink density determines the amount of ink deposited on the material. Adjusting this setting can impact color vibrancy and overall print quality.
Test Prints: Conduct test prints with varying ink densities to find the optimal setting. Too little ink can result in faded colors, while too much ink may cause bleeding or smudging.
Material Considerations: Different materials absorb ink differently. For example, porous materials like wood may require higher ink densities to achieve rich colors, whereas non-porous materials like glass might need lower densities to prevent ink pooling.
3. Print Speed
While faster print speeds can increase productivity, they may compromise print quality if not properly balanced with other settings.
Quality vs. Speed: For the best results, find a balance between speed and quality. Slower print speeds usually allow for better ink deposition and curing, resulting in higher-quality prints.
Material Handling: Ensure the printer’s speed does not cause material shifting or ink misalignment, especially with lighter or flexible substrates.
4. Curing Settings
The UV curing process is crucial for ink adherence and durability. Proper adjustment of curing settings ensures the ink is fully cured and bonds correctly with the material.
UV Intensity: Higher UV intensity can cure ink more quickly but may require fine-tuning to prevent over-curing, which can cause cracking or discoloration.
Curing Time: The amount of time the ink is exposed to UV light must be adequate for a complete cure. This can vary based on ink type, material, and ink density.
Test Cures: Perform test cures to determine the optimal combination of UV intensity and exposure time for your specific application.
5. Color Management
Achieving accurate colors requires proper color management settings.
Color Profiles: Use ICC (International Color Consortium) profiles specific to your printer, inks, and materials to ensure color accuracy.
Calibration: Regularly calibrate your printer to maintain consistent color output.
Color Matching: Utilize color-matching software to adjust and fine-tune colors until they match your desired outcome.
6. Print Heads and Height Adjustment
The distance between the print heads and the material (print head gap) can affect ink deposition and print quality.
Optimal Gap: Refer to your printer’s manual for recommended print head gaps for different materials and thicknesses.
Automatic Adjustments: Many modern UV flatbed printers feature automatic height adjustment sensors that detect material thickness and adjust the print head gap accordingly.
7. Nozzle Size and Configuration
Different nozzle sizes affect the ink droplet size and, consequently, the print quality and speed.
Fine Nozzles: Smaller nozzles produce finer details but may slow down the printing process.
Larger Nozzles: Larger nozzles deposit more ink quickly, which is ideal for covering larger areas but may sacrifice some detail.
8. Material Handling and Support
Ensuring the material is securely positioned and supported during printing prevents movement and ensures precise ink deposition.
Fixtures and Jigs: Use fixtures or jigs to hold materials in place, especially if they are irregularly shaped or flexible.
Vacuum Tables: Many UV flatbed printers are equipped with vacuum tables that hold materials flat and secure during printing.
9. Software Settings
The printer’s software offers various settings that can be adjusted for optimal print quality.
Rip Software: Use RIP (Raster Image Processor) software to manage and optimize print jobs. This software can adjust settings such as resolution, color management, and ink usage.
Print Modes: Choose the appropriate print mode based on your requirements. For example, “high-quality” mode for detailed prints or “draft” mode for quick, low-resolution prints.
10. Maintenance and Cleaning
Regular maintenance and cleaning of the printer ensure consistent and high-quality prints.
Nozzle Cleaning: Regularly clean print heads to prevent clogs and maintain ink flow.
UV Lamp Maintenance: Check and replace UV lamps as needed to ensure they are functioning at full intensity.
Daily Inspections: Perform daily inspections of the printer to identify and address any potential issues before they affect print quality.
Best Practices for Achieving Optimal Print Results
Conduct Regular Test Prints: Regularly print test samples to monitor print quality and make adjustments as needed.
Use High-Quality Materials: Invest in high-quality inks and substrates to ensure the best possible prints.
Stay Updated: Keep your printer’s firmware and software up-to-date to benefit from the latest improvements and features.
Operator Training: Ensure that operators are well-trained in all aspects of the printer’s operation and maintenance.
Environment Control: Maintain a clean and controlled environment to prevent dust and debris from affecting print quality.
Achieving the best results with a UV flatbed printer requires careful adjustment of multiple settings and a good understanding of both the printer’s capabilities and the materials being printed on. By fine-tuning resolution, ink density, print speed, curing settings, color management, print head gap, nozzle size, material handling, software settings, and maintenance, you can ensure high-quality prints with vibrant colors and sharp details. Regular test prints, the use of high-quality materials, and ongoing operator training are essential practices that will help maintain optimal print quality and productivity. With the right adjustments and practices, your UV flatbed printer can produce outstanding prints that meet or exceed your expectations.