UV Flatbed Printer: How to Achieve Vibrant and Saturated Colors
UV Flatbed Printer: How to Achieve Vibrant and Saturated Colors
In the realm of digital printing, achieving vibrant and saturated colors is paramount to producing visually appealing and impactful prints. Among the various printing technologies available, UV flatbed printers have gained significant popularity due to their ability to deliver exceptional color quality on a wide range of substrates. This article delves into the intricacies of UV flatbed printing and provides comprehensive insights on how to achieve those desirable, eye-catching colors.
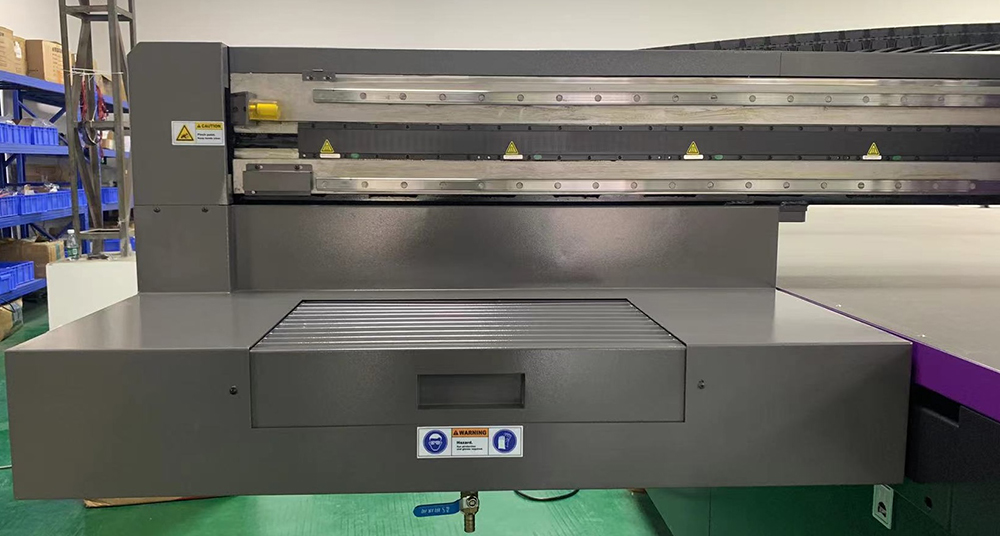
Understanding UV Flatbed Printing
UV flatbed printing is a form of digital printing that utilizes ultraviolet (UV) light to cure or dry the ink instantly after it is applied to the substrate. This technology allows for printing on various materials, including rigid substrates like glass, metal, wood, and plastics, as well as flexible materials like vinyl and fabric. The UV-curable inks used in these printers offer numerous advantages, such as durability, resistance to fading, and the ability to produce vivid colors.
The Importance of Color Vibrancy and Saturation
Color vibrancy refers to the purity and intensity of a color, while saturation denotes the richness or strength of a color’s hue. In graphic design and printing, achieving high levels of both is crucial for several reasons:
Visual Impact: Vibrant and saturated colors capture attention and create a lasting impression.
Brand Representation: Accurate color representation is essential for maintaining brand integrity.
Emotional Response: Colors evoke emotions; vibrant hues can convey energy, excitement, and professionalism.
Quality Perception: High-quality prints with rich colors are often perceived as more valuable and professional.
Factors Affecting Color Vibrancy and Saturation
Several factors influence the color output of a UV flatbed printer. Understanding these factors is key to optimizing your prints for the best possible color quality.
1. Ink Quality
The quality of the UV-curable ink is foundational. Premium inks contain higher concentrations of pigments, which contribute to better color saturation and vibrancy. Additionally, inks with smaller particle sizes can produce smoother and more uniform color coverage.
Pigment Concentration: Higher pigment loads result in richer, more saturated colors.
Ink Viscosity: Proper viscosity ensures even ink distribution and better color consistency.
2. Printer Calibration
Regular calibration of the UV flatbed printer is crucial for maintaining color accuracy. Calibration involves adjusting the printer’s settings to ensure that the colors it produces match the intended colors on screen.
Color Profiles: Using appropriate ICC (International Color Consortium) profiles for different substrates can significantly improve color accuracy.
Linearization: Adjusting the printer’s response to different ink densities ensures a consistent color output across the entire print.
3. Substrate Choice
The type and color of the substrate can dramatically affect the appearance of the printed colors. Different materials absorb and reflect ink differently, influencing the final color saturation and vibrancy.
Absorption Rate: Materials with high absorption rates may require more ink to achieve saturation.
Surface Texture: Smooth surfaces tend to reflect light better, enhancing color vibrancy.
4. Print Resolution
The resolution of the printer, measured in dots per inch (DPI), directly impacts the clarity and sharpness of the print, indirectly affecting color perception.
Higher Resolution: More dots per inch result in finer details and smoother color transitions.
Ink Drop Size: Smaller ink drops can produce more precise and vibrant colors.
5. UV Curing Process
The UV curing process itself can affect color development. Proper curing ensures that the ink adheres correctly to the substrate and fully develops its color.
Curing Intensity: Too much or too little UV exposure can alter the color’s appearance.
Curing Speed: Faster curing times may require adjustments to ink formulation and application to maintain color quality.
Techniques to Achieve Vibrant and Saturated Colors
Achieving optimal color vibrancy and saturation with a UV flatbed printer involves a combination of technical adjustments and best practices. Here are some effective techniques:
1. Use High-Quality Inks
Investing in premium UV-curable inks is one of the most direct ways to enhance color vibrancy. Look for inks with high pigment concentrations and small particle sizes for the best results.
2. Optimize Printer Settings
Color Management: Utilize advanced color management tools to ensure accurate color matching.
Ink Density: Adjust ink density settings to achieve the desired color saturation without over-applying ink, which can lead to smudging or bleeding.
3. Choose the Right Substrate
Color and Texture: Select substrates that complement the colors you intend to print. Lighter-colored or white substrates will generally make colors appear more vibrant.
Pre-Treatment: Some substrates may require pre-treatment to improve ink adhesion and color saturation.
4. Calibrate Regularly
Monthly Calibration: At a minimum, calibrate your printer monthly, or more frequently if you notice color shifts.
Profile Updates: Regularly update your ICC profiles to account for any changes in ink, substrate, or environmental conditions.
5. Fine-Tune the Curing Process
Curing Lamp Adjustment: Adjust the intensity and duration of UV exposure to ensure proper ink curing without compromising color quality.
Test Prints: Conduct test prints with varying curing settings to find the optimal balance for your specific ink and substrate combination.
6. Utilize Color Enhancement Software
RIP Software: Raster image processors (RIPs) can optimize images for printing, enhancing color saturation and vibrancy.
Color Correction: Use color correction tools within your design software to adjust hues, saturation, and brightness before printing.
7. Maintain Printer Cleanliness
Nozzle Cleaning: Regularly clean printer nozzles to prevent clogs and ensure consistent ink flow.
Print Head Alignment: Keep the print heads aligned for precise ink placement and avoid color bleeding.
Conclusion
Achieving vibrant and saturated colors with a UV flatbed printer is a multifaceted process that involves careful selection of inks, substrates, and printer settings, as well as regular maintenance and calibration. By understanding the factors that influence color output and implementing the techniques outlined in this article, you can produce prints that are not only visually striking but also of the highest quality. Whether you’re printing marketing materials, artistic creations, or signage, mastering the art of color vibrancy and saturation will set your work apart and leave a lasting impression.
In summary, the key to successful UV flatbed printing lies in meticulous attention to detail, from ink selection to final curing. By following the guidelines provided, you can harness the full potential of your UV flatbed printer and create prints that truly stand out with their vibrant and saturated colors.