Technical Overview: UV Flatbed Printer Mechanisms
Technical Overview: UV Flatbed Printer Mechanisms
In today’s rapidly evolving digital printing industry, UV flatbed printers have emerged as a game-changer, offering unparalleled precision, versatility, and cost-effectiveness. This technical overview delves into the intricacies of UV flatbed printer mechanisms, exploring their core components, operational principles, and advanced features that make them a preferred choice for a wide range of industries.
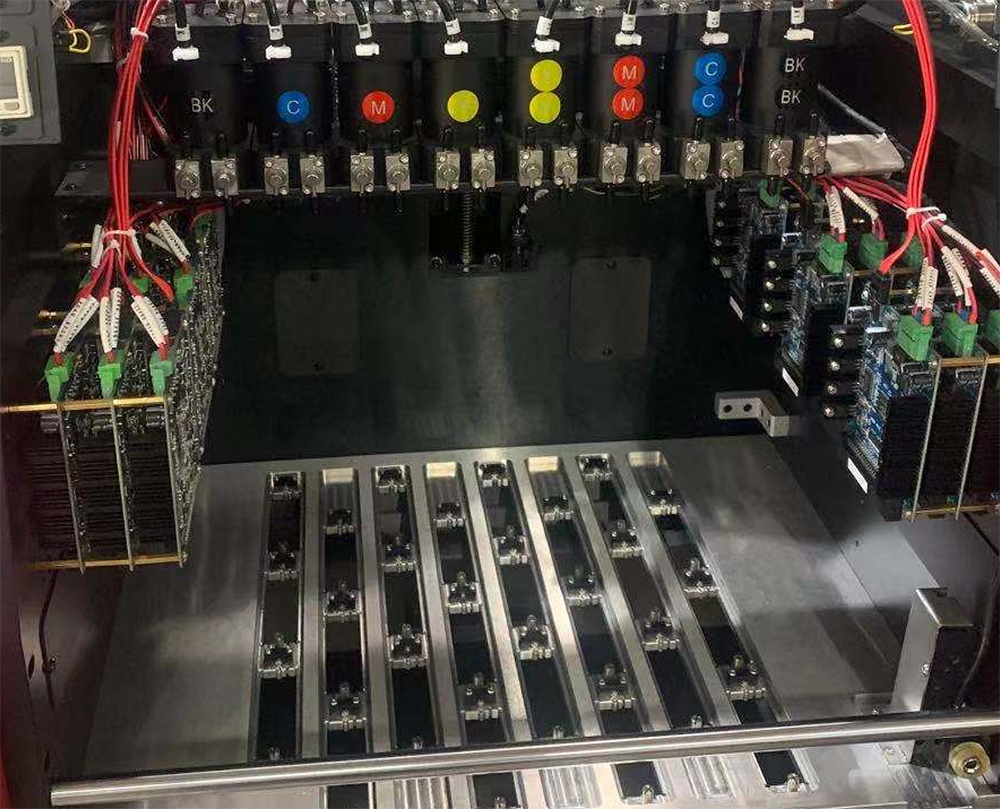
Introduction
UV flatbed printers represent the cutting edge of digital printing technology. They combine the precision of inkjet printing with the durability and versatility of UV-cured inks, enabling the production of high-quality graphics on various materials and surfaces. This technology has revolutionized the advertising, packaging, signage, and manufacturing sectors by offering a fast, flexible, and cost-effective alternative to traditional printing methods.
Core Components of UV Flatbed Printers
1. Print Heads and Ink System
At the heart of every UV flatbed printer lies the print head, responsible for delivering the ink onto the print media. Advanced models, such as those equipped with Ricoh print heads imported from Japan, offer variable droplet technology that enables precise control over ink droplet size. This technology, known as VersaDrop, allows for full grayscale printing without compromising on production speed, resulting in images with photo-realistic quality and exceptional detail.
The ink system is designed to accommodate UV-cured inks, which cure instantly upon exposure to UV light. These inks offer superior durability and scratch resistance, making them ideal for outdoor applications and materials that require high abrasion resistance. The ink system is typically closed-loop, ensuring continuous ink circulation to prevent clogging and maintain consistent print quality.
2. UV Curing System
UV flatbed printers employ UV-LED curing systems that instantly cure the ink as it is deposited on the print media. This process not only accelerates the drying time but also enhances the ink’s adhesion and durability. The UV-LED curing system is energy-efficient and environmentally friendly, emitting minimal heat and UV radiation during operation.
3. Motion Control System
The motion control system is responsible for the precise positioning of the print head relative to the print media. It typically comprises linear guides, stepper motors, and encoders that ensure smooth and accurate movement. The use of metal or plastic optical gratings (such as those manufactured by Renishaw) further enhances positional accuracy, allowing for precise registration and repeatability.
4. Print Bed and Media Handling
The print bed is where the media is placed during the printing process. UV flatbed printers often feature vacuum tables or mechanical clamps to secure the media in place, ensuring that it remains flat and stable throughout the printing process. Some models also offer automatic media loading and unloading systems to streamline production workflows.
Operational Principles
UV flatbed printers operate on a straightforward yet highly sophisticated principle. The process begins with the loading of the print media onto the print bed, where it is secured in place. The ink system is then activated, and the print head begins depositing ink onto the media in a precise, controlled manner.
As the ink is deposited, the UV curing system simultaneously exposes the ink to UV light, causing it to cure instantly. This process continues until the entire image is printed, after which the media is unloaded from the printer and ready for further processing or installation.
Advanced Features and Benefits
1. Versatility
UV flatbed printers are renowned for their versatility, capable of printing on a wide range of materials and surfaces. This includes flexible media such as vinyl, textiles, and paper, as well as rigid substrates like glass, metal, and wood. The ability to print directly onto these materials eliminates the need for intermediate substrates or transfer processes, saving time and cost.
2. Precision and Quality
With resolutions reaching up to 1200dpi and beyond, UV flatbed printers deliver images with photo-realistic quality and exceptional detail. The precision of the print heads and the accuracy of the motion control system ensure that every print is registered precisely and consistently, even at high speeds.
3. Cost-Effectiveness
UV flatbed printers offer a cost-effective alternative to traditional printing methods, particularly for short-run and custom jobs. Their ability to print directly onto a variety of media eliminates the need for expensive printing plates or screens, significantly reducing setup costs and lead times.
4. Environmental Friendliness
UV flatbed printers are environmentally friendly, emitting minimal VOCs (volatile organic compounds) during operation. The use of UV-cured inks further reduces the environmental impact, as they cure instantly and do not require drying or washing processes that consume large amounts of water and energy.
5. High Productivity
Advanced UV flatbed printers are designed for high productivity, capable of printing at speeds that rival or exceed those of traditional printing methods. Their ability to handle a wide range of media and print in full color without the need for screens or plates makes them an ideal solution for high-volume production environments.
Advanced Technologies and Innovations
1. Inkjet Color Management
UV flatbed printers employ advanced color management technologies to ensure accurate color reproduction across various media types and applications. These technologies include GCR (gray component replacement) color management, high-precision spot color matching, and automatic color balancing. These features ensure that every print is consistent and meets the highest standards of color accuracy.
2. RediJet Ink Circulation System
Some UV flatbed printers feature the RediJet ink circulation system, which continuously circulates ink through the print head to prevent clogging and maintain consistent print quality. This system significantly reduces downtime and maintenance requirements, allowing for uninterrupted printing and increased productivity.
3. VersaDrop Variable Droplet Technology
As mentioned earlier, VersaDrop variable droplet technology enables precise control over ink droplet size, allowing for full grayscale printing without compromising on production speed. This technology enhances the printer’s ability to produce high-quality images with smooth gradients and exceptional detail.
4. Advanced Media Handling
Advanced UV flatbed printers often feature sophisticated media handling systems that can accommodate various media types and sizes. These systems include vacuum tables with adjustable zones, mechanical clamps, and automatic media loading and unloading systems. These features ensure that every print is registered precisely and consistently, even on challenging media types and surfaces.
Conclusion
UV flatbed printers represent the future of digital printing technology. Their combination of precision, versatility, and cost-effectiveness makes them an ideal solution for a wide range of industries, including advertising, packaging, signage, and manufacturing. As these printers continue to evolve and incorporate advanced technologies, their potential for innovation and growth remains unlimited.
In summary, UV flatbed printers offer a powerful and flexible solution for high-quality digital printing on a wide range of materials and surfaces. Their advanced features, including variable droplet technology, UV curing systems, and precise motion control, ensure that every print is registered precisely and consistently, delivering images with photo-realistic quality and exceptional detail. As these printers continue to advance, they will undoubtedly play an increasingly important role in the digital printing industry for years to come.