Technical Insights: UV-Curable Ink Composition and Properties
Technical Insights: UV-Curable Ink Composition and Properties
Ultraviolet (UV)-curable inks have become increasingly popular in various industrial applications due to their numerous advantages over conventional inks. These advantages include fast cure speeds, low energy consumption, no volatile organic compounds (VOCs), and excellent adhesion to a wide range of substrates. This article provides an in-depth analysis of UV-curable ink compositions and their properties, highlighting the key components, preparation methods, and performance characteristics.
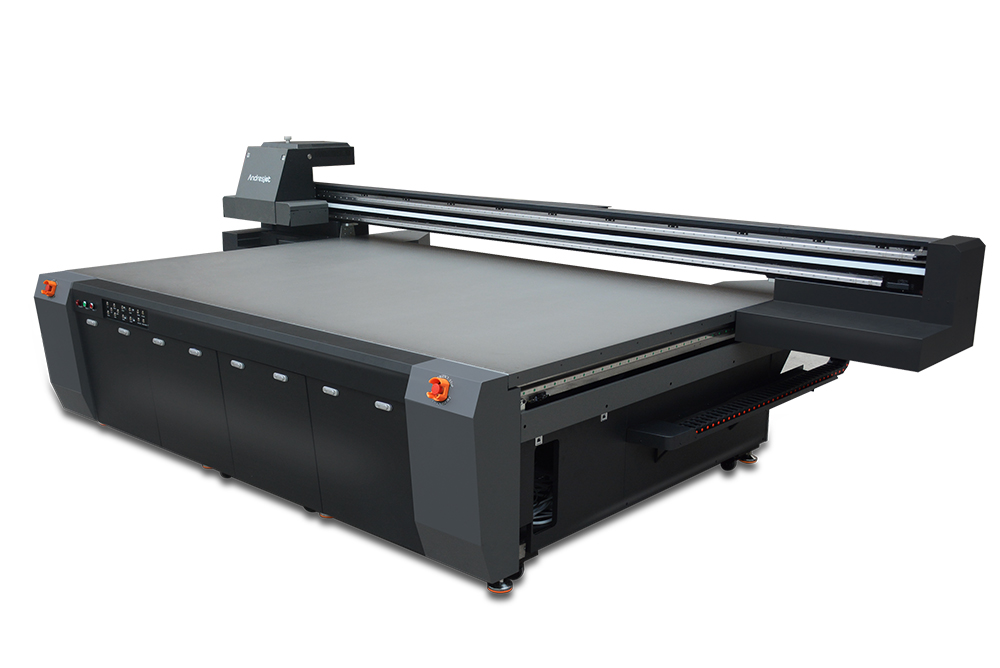
Composition of UV-Curable Ink
UV-curable inks are formulated to undergo rapid polymerization when exposed to UV light, transforming from a liquid state to a solid state. The composition of UV-curable inks typically includes the following key components:
Light-Sensitive Resins
Light-sensitive resins, also known as prepolymers, are the backbone of UV-curable inks. They are responsible for the formation of the cross-linked polymer network upon UV exposure. Commonly used light-sensitive resins include epoxy acrylates, urethane acrylates, polyester acrylates, and polyether acrylates. The choice of resin depends on the desired properties of the cured ink, such as flexibility, hardness, and adhesion.
Active Monomers
Active monomers, or diluents, are used to adjust the viscosity of the ink and participate in the polymerization process. They are generally low molecular weight compounds that can react with the light-sensitive resins under UV light. Examples of active monomers include mono-functional and multi-functional acrylates, methacrylates, and vinyl ethers. The ratio of active monomers to light-sensitive resins significantly affects the cure speed and physical properties of the cured ink.
UV Light Initiators
UV light initiators are essential for initiating the polymerization reaction. They absorb UV light and generate free radicals or cations that initiate the cross-linking of the prepolymers and active monomers. Commonly used UV light initiators include benzophenones, acetophenones, thioxanthones, and phosphine oxides. The choice of initiator depends on the type of UV light source and the desired cure speed.
Pigments
Pigments are added to UV-curable inks to provide color. They are finely ground solid particles that are dispersed uniformly in the ink. The choice of pigment affects the color strength, opacity, and weatherability of the cured ink. Commonly used pigments include organic and inorganic pigments such as titanium dioxide, carbon black, and phthalocyanine blue.
Additives
Additives are used to enhance the performance of UV-curable inks. Examples include flow control agents, defoamers, and stabilizers. Flow control agents improve the leveling and wetting properties of the ink, while defoamers prevent the formation of bubbles during ink preparation and application. Stabilizers protect the ink against degradation caused by UV light and oxygen.
Preparation Methods
The preparation of UV-curable inks involves several steps, including resin selection, formulation design, and dispersion.
Resin Selection
The selection of light-sensitive resins is critical for achieving the desired properties of the cured ink. Factors such as flexibility, hardness, and adhesion must be considered. For example, urethane acrylates are often chosen for their excellent flexibility and adhesion to a variety of substrates.
Formulation Design
The formulation design involves determining the ratios of the various components, such as light-sensitive resins, active monomers, UV light initiators, pigments, and additives. These ratios are adjusted to achieve the desired viscosity, cure speed, and physical properties of the cured ink.
Dispersion
Dispersion is the process of uniformly dispersing the pigments and additives in the ink. This is typically achieved using high-shear mixers or ball mills. Proper dispersion is crucial for ensuring good color strength, opacity, and stability of the ink.
Properties of UV-Curable Ink
UV-curable inks exhibit a range of properties that make them suitable for various applications. These properties include cure speed, adhesion, flexibility, hardness, and weatherability.
Cure Speed
Cure speed is the rate at which the ink transforms from a liquid state to a solid state upon UV exposure. It is affected by the type and concentration of UV light initiators, the intensity of the UV light source, and the formulation of the ink. Fast cure speeds are desirable for increasing production efficiency and reducing energy consumption.
Adhesion
Adhesion refers to the ability of the cured ink to adhere to the substrate. It is influenced by the choice of light-sensitive resins, the surface energy of the substrate, and the presence of adhesion promoters. Good adhesion is crucial for ensuring the durability and reliability of the printed product.
Flexibility
Flexibility is the ability of the cured ink to withstand bending or flexing without cracking or breaking. It is determined by the type and concentration of light-sensitive resins, as well as the ratio of active monomers to light-sensitive resins. Flexible inks are suitable for applications on curved or deformable substrates.
Hardness
Hardness refers to the resistance of the cured ink to scratching or abrasion. It is influenced by the choice of light-sensitive resins, the ratio of active monomers to light-sensitive resins, and the presence of hardeners. Hard inks are suitable for applications where durability and wear resistance are required.
Weatherability
Weatherability is the ability of the cured ink to withstand exposure to sunlight, moisture, and temperature extremes without fading or deteriorating. It is influenced by the choice of pigments, UV light initiators, and stabilizers. Good weatherability is important for applications in outdoor environments.
Applications of UV-Curable Ink
UV-curable inks are used in a wide range of applications across various industries.
Printing and Packaging
UV-curable inks are commonly used in printing and packaging applications due to their fast cure speeds, low energy consumption, and excellent adhesion to a variety of substrates. They are suitable for flexographic, gravure, screen, and inkjet printing processes.
Electronics
UV-curable inks are used in the manufacture of electronic components such as printed circuit boards, touch screens, and solar cells. They provide high resolution, good electrical conductivity, and excellent adhesion to the substrate.
Automotive
UV-curable inks are used in automotive applications for marking, labeling, and decorative purposes. They are resistant to weathering, abrasion, and chemicals, making them suitable for exterior and interior components.
Medical
UV-curable inks are used in medical applications for marking and labeling medical devices and packaging. They are biocompatible, non-toxic, and resistant to sterilization processes.
UV-curable inks offer numerous advantages over conventional inks, making them suitable for a wide range of applications across various industries. The composition of UV-curable inks is carefully designed to achieve the desired properties, such as cure speed, adhesion, flexibility, hardness, and weatherability. With continuous advancements in resin technology and formulation design, UV-curable inks are expected to play an increasingly important role in the future of printing and coating technologies.