Technical Insights into the Design of Modern UV Flatbed Printers
In the realm of digital printing, UV flatbed printers have emerged as a game-changer, revolutionizing the way images and graphics are applied to a myriad of surfaces. These versatile machines have found their niche in various industries, ranging from advertising and signage to packaging and decorative arts. The essence of their success lies in their ability to print on virtually any material, from rigid substrates like glass, metal, and ceramics to flexible media such as fabrics and vinyl, all while delivering high-resolution outputs with exceptional durability. This article delves into the technical intricacies that underpin the design of modern UV flatbed printers, shedding light on the key components, innovative technologies, and design philosophies that contribute to their superior performance.
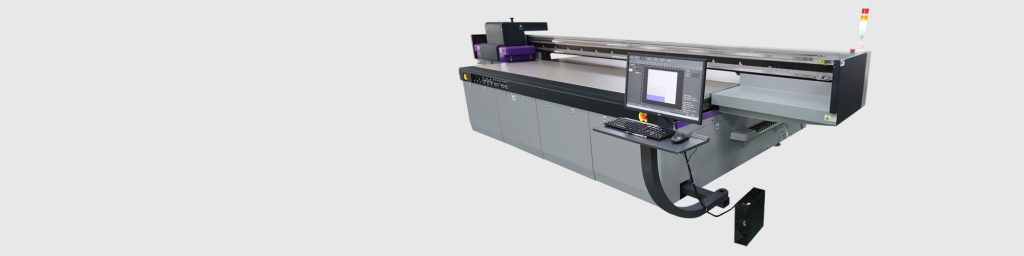
1. UV-Curable Inks: The Cornerstone of Quality
At the heart of every UV flatbed printer lies the ink. Unlike traditional solvent or aqueous inks, UV-curable inks are formulated to solidify almost instantly upon exposure to ultraviolet light. This rapid curing process not only accelerates production times but also ensures that the ink adheres firmly to the substrate, creating a durable and scratch-resistant finish. The composition of UV inks includes photoinitiators, oligomers, monomers, and pigments, carefully balanced to achieve optimal print quality, adhesion, and flexibility.
The choice of ink chemistry is crucial, as it directly impacts the printer’s versatility and the range of materials it can handle. For instance, some inks are designed to flex with the substrate, making them ideal for applications where the printed item will be bent or folded. Others are engineered for superior chemical resistance, suiting them to outdoor signage or industrial labeling where exposure to harsh elements is expected.
2. LED UV Curing Systems: Efficiency and Precision
Traditional UV printers employed mercury vapor lamps for curing, but modern designs have largely transitioned to LED-based systems. LED UV curing offers several advantages over its predecessor, including lower energy consumption, longer lifespan, and reduced heat generation. These benefits translate into cost savings, environmental friendliness, and the ability to maintain a stable printing environment, which is critical for precise ink deposition.
Moreover, LED UV systems can be precisely controlled, allowing for variable curing intensities tailored to different inks and substrates. This level of control ensures that the ink cures correctly, minimizing the risk of over- or under-curing, which can lead to poor adhesion or surface distortion.
3. Precision Printheads: The Art of Detail
The printhead is the workhorse of any UV flatbed printer, responsible for depositing ink with exceptional accuracy. Modern printers utilize advanced piezoelectric or thermal inkjet technologies, each with its own set of advantages. Piezoelectric printheads offer high precision and reliability, making them suitable for detailed graphics and fine text. Thermal inkjet heads, on the other hand, are known for their cost-effectiveness and ability to handle a wide range of ink viscosities.
Regardless of the technology, the key to outstanding print quality lies in the printhead’s ability to eject ink droplets of consistent size and trajectory. Manufacturers invest heavily in research and development to optimize nozzle design, ink flow dynamics, and drive electronics, ensuring that each droplet lands precisely where intended, even at high printing speeds.
4. Rigid and Flexible Media Handling: Adaptability at Its Best
One of the defining features of UV flatbed printers is their ability to handle both rigid and flexible media. This adaptability is achieved through sophisticated media handling systems that can securely hold and transport substrates of varying thicknesses and textures. For rigid materials, vacuum tables are commonly used, which employ a series of suction cups to keep the substrate firmly in place during printing. Flexible media, on the other hand, are often guided through the printer using rollers and tension control mechanisms to ensure smooth and wrinkle-free printing.
The design of these handling systems must account for the unique challenges posed by different materials. For example, printing on uneven or textured surfaces requires adjustable vacuum pressure and conformal printheads that can maintain consistent ink deposition despite variations in surface height.
5. Advanced Software and RIP Technologies: Bridging Creativity and Precision
Behind every stunning print lies powerful software that translates digital designs into precise printing instructions. Raster Image Processors (RIPs) play a pivotal role in this process, converting vector graphics and images into a bitmap format that the printer can understand. Modern RIP software not only optimizes image quality but also offers advanced color management, variable data printing capabilities, and nesting features that maximize material utilization.
Furthermore, some UV flatbed printers come equipped with sophisticated workflow management systems that streamline the printing process from design to output. These systems can automate tasks such as job scheduling, media loading, and quality control, reducing operator intervention and increasing productivity.
6. Environmental Considerations: Green Printing Practices
As environmental consciousness grows, so does the demand for greener printing solutions. Modern UV flatbed printers are designed with sustainability in mind, employing inks that are free from volatile organic compounds (VOCs) and utilizing energy-efficient components. Additionally, the ability to cure inks instantly reduces the need for drying ovens, further cutting down on energy consumption and carbon emissions.
Manufacturers are also exploring ways to recycle and dispose of used inks and substrates responsibly, minimizing the environmental impact of the printing process. Some printers even feature ink recovery systems that capture and reuse excess ink, reducing waste and lowering operational costs.
The design of modern UV flatbed printers is a testament to the fusion of cutting-edge technology and innovative engineering. From the development of UV-curable inks and LED curing systems to the precision of printheads and the adaptability of media handling systems, every aspect of these printers is meticulously crafted to deliver unparalleled print quality, versatility, and efficiency.
As the digital printing industry continues to evolve, so too will the design of UV flatbed printers. Future advancements may include even more sustainable ink formulations, smart automation technologies, and integrated quality control systems that push the boundaries of what is possible in digital printing. For now, however, it is clear that modern UV flatbed printers are at the forefront of innovation, enabling businesses to bring their creative visions to life with precision, efficiency, and environmental responsibility.