Technical Insights into Color Management in UV Flatbed Printing
Technical Insights into Color Management in UV Flatbed Printing
UV flatbed printing, a popular technique in the digital printing industry, offers numerous advantages such as high-quality output, versatility in substrate handling, and rapid production speeds. Central to achieving consistent and accurate color reproduction in this printing process is effective color management. This article delves into the technical aspects of color management in UV flatbed printing, exploring key concepts, challenges, and strategies for optimal color control.
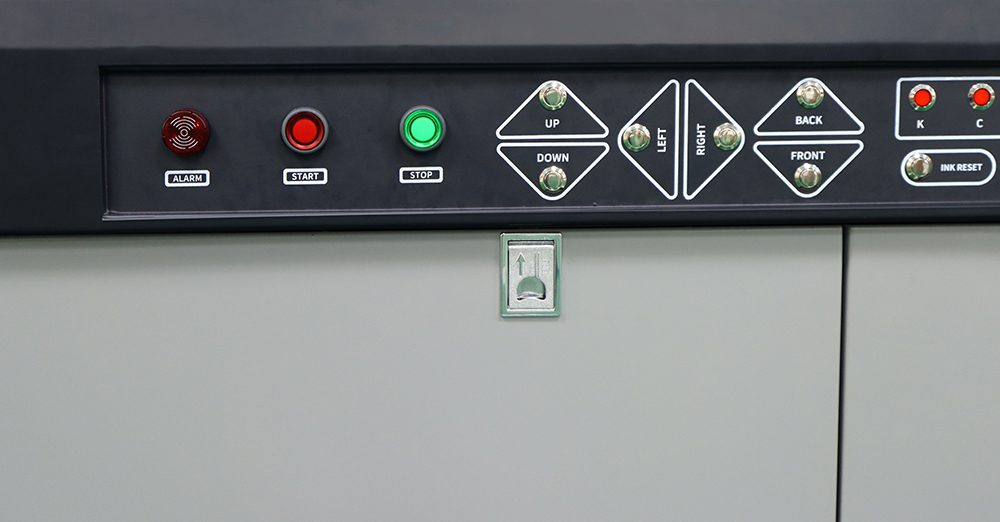
Understanding Color Management
Color management is a systematic approach to controlling and coordinating colors across different devices and media. It ensures that the colors in a digital image remain consistent throughout the entire printing process, from design to final output. In UV flatbed printing, color management involves several critical steps, including color profiling, calibration, and color correction.
Color Profiling
Color profiling is the foundation of color management. It involves creating a color profile, which is a set of data that describes the color characteristics of a specific device or substrate. For UV flatbed printers, this includes understanding how the printer’s inks interact with various materials and how the UV curing process affects color output.
ICC (International Color Consortium) profiles are commonly used in the printing industry. They define the color gamut of a device, describing how it reproduces colors and how those colors should be adjusted to achieve accurate results. Creating custom ICC profiles for UV flatbed printers involves measuring a large number of color samples printed on different substrates and then using software to generate a profile that maps the printer’s color space to a standard color space, such as CIELAB.
Calibration and Maintenance
Regular calibration is essential to maintain consistent color output in UV flatbed printing. Calibration involves adjusting the printer’s settings to ensure that it reproduces colors accurately according to its color profile. This process typically involves printing a test target with a range of colors and then measuring those colors using a spectrophotometer or colorimeter. The measurement data is then used to adjust the printer’s settings to minimize color deviations.
In addition to calibration, proper maintenance of the printer is crucial. This includes regular cleaning of the printhead, ink system, and UV lamps to prevent color shifts caused by ink residue or lamp degradation. Environmental factors, such as temperature and humidity, can also affect color output and should be monitored and controlled.
Color Correction and Enhancement
Color correction is often necessary to achieve the desired color appearance in UV flatbed printing. This involves adjusting the digital image file before printing to compensate for any color shifts that may occur during the printing process. Color correction can be performed using image editing software, such as Adobe Photoshop, which allows for precise adjustments to color balance, saturation, and brightness.
In some cases, color enhancement techniques may also be used to improve the visual impact of the printed image. This can involve increasing color vibrancy, adjusting contrast, or applying special effects to enhance certain colors or features in the image.
Challenges in UV Flatbed Printing Color Management
Despite the advancements in color management technology, several challenges remain in achieving consistent and accurate color reproduction in UV flatbed printing. These challenges include:
Substrate Variability: Different substrates can have varying absorption and reflection properties, which can affect how inks adhere and cure, leading to color shifts.
Ink Interactions: The chemical composition of UV inks can interact with certain substrates, causing unexpected color changes.
UV Curing Effects: The UV curing process can cause inks to shrink or change color slightly as they cure, requiring careful control to maintain color accuracy.
Environmental Factors: Temperature, humidity, and even air quality can impact ink curing and color reproduction.
Printer Calibration Drift: Even with regular calibration, printers can experience drift in color accuracy over time due to wear and tear or changes in ink chemistry.
Strategies for Effective Color Management
To overcome these challenges and achieve optimal color management in UV flatbed printing, the following strategies can be employed:
Substrate Testing: Conduct thorough testing of different substrates to understand their color reproduction characteristics and develop specific color profiles for each.
Ink Selection and Management: Choose inks that are compatible with the substrates being used and establish strict ink management protocols to ensure consistent ink quality.
Environmental Control: Maintain a stable printing environment with controlled temperature and humidity levels to minimize environmental impact on color output.
Advanced Calibration Techniques: Use advanced calibration tools and techniques, such as iterative profiling and G7 calibration, to achieve higher levels of color accuracy.
Software Solutions: Leverage color management software that can automate color correction and profiling tasks, reducing manual intervention and potential errors.
Operator Training: Train printing operators on color management principles and best practices to ensure consistent implementation of color management protocols.
Conclusion
Color management in UV flatbed printing is a complex but essential process for achieving accurate and consistent color reproduction. By understanding the technical aspects of color profiling, calibration, and correction, and by implementing effective strategies to overcome the challenges inherent in this printing process, printers can deliver high-quality prints that meet the demanding standards of today’s market. As technology continues to evolve, so too will the capabilities of color management in UV flatbed printing, further enhancing its position as a versatile and valuable tool in the digital printing industry.