Technical Challenges in Printing on Non-Porous Materials with a UV Flatbed Printer
Technical Challenges in Printing on Non-Porous Materials with a UV Flatbed Printer
In the realm of digital printing, UV flatbed printers have revolutionized the way we approach printing on a wide array of substrates. Among the myriad of materials that can be printed on, non-porous surfaces pose a unique set of challenges. Unlike porous materials such as paper or fabric, which absorb ink readily, non-porous materials like glass, metal, plastic, and certain types of coated surfaces repel ink, making the printing process more complex. This article delves into the technical challenges encountered when printing on non-porous materials using a UV flatbed printer and explores strategies to overcome these hurdles.
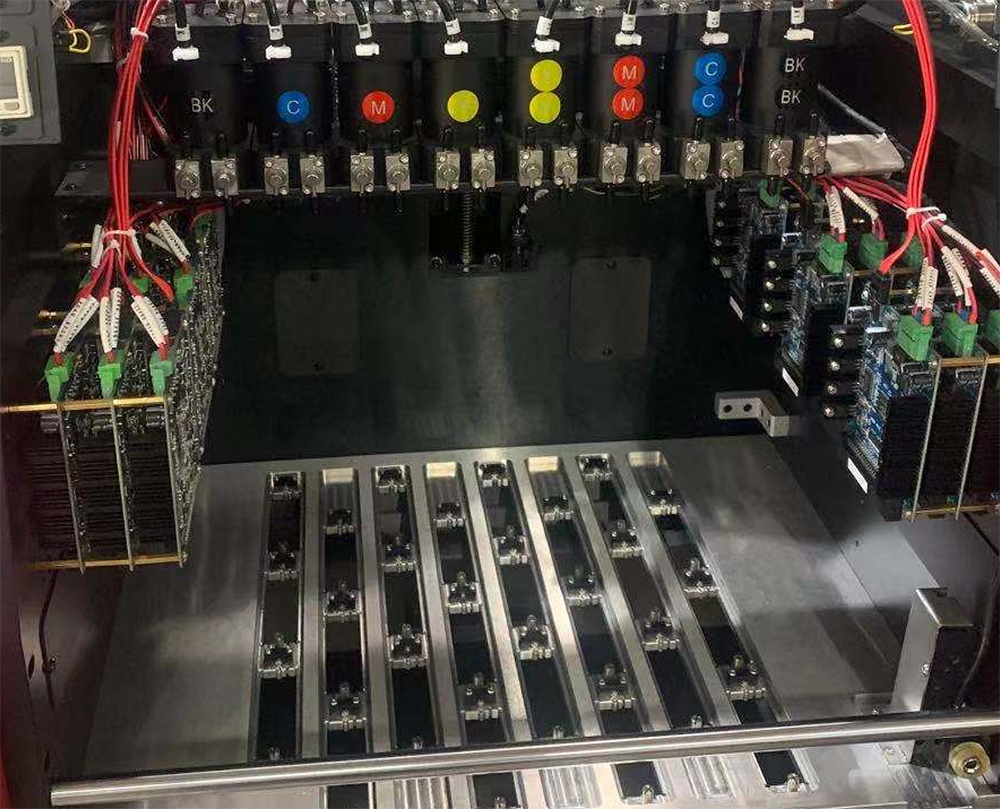
Understanding Non-Porous Materials
Non-porous materials are characterized by their lack of pores or absorbent spaces, which means they do not allow liquids to penetrate easily. This property makes them ideal for applications where durability and resistance to moisture or chemicals are required. However, it also presents a significant barrier for ink adhesion, as traditional inks rely on absorption to bond with the substrate.
UV inks, used in UV flatbed printers, are designed to cure instantly upon exposure to ultraviolet light. This rapid curing process eliminates the need for absorption, as the ink is solidified almost immediately after being applied. Despite this advantage, printing on non-porous materials still involves several technical challenges that must be addressed to ensure high-quality prints.
Adhesion Issues
One of the primary challenges in printing on non-porous materials is achieving proper ink adhesion. Since these materials do not absorb ink, the ink must form a strong mechanical bond with the surface. This requires a meticulous balance between ink viscosity, surface tension, and the printer’s ability to deposit the ink uniformly.
To improve adhesion, printers often employ special primers or adhesion promoters. These substances are applied to the substrate before printing and create a microscopic texture that the ink can adhere to. Choosing the right primer is crucial, as it must be compatible with both the substrate and the UV ink. Incorrect primer selection can lead to poor adhesion, ink peeling, or even damage to the substrate.
Moreover, the printing process itself must be fine-tuned. Adjusting parameters such as ink pressure, print speed, and the distance between the print head and the substrate can significantly affect ink adhesion. Too high a pressure can cause the ink to splatter, while too low a pressure may result in incomplete coverage. Similarly, an optimal print speed ensures that the ink is deposited evenly without compromising its ability to cure properly.
Ink Spreading and Bleeding
Another challenge specific to non-porous materials is ink spreading and bleeding. Unlike porous surfaces that contain ink within their fibers, non-porous surfaces allow ink to spread more freely. This can lead to blurry prints, color bleeding, and loss of detail.
To mitigate this issue, UV inks are formulated with higher viscosity and faster curing times. High-viscosity inks are less likely to spread, and rapid curing minimizes the time ink has to move on the surface. However, this also means that the printing process must be precisely controlled. Any delay in curing can cause the ink to spread, while excessive curing can lead to over-hardening and cracking.
Printer manufacturers have developed advanced print heads with finer nozzles and more precise ink droplet control to address this challenge. These print heads can deposit ink with greater accuracy, reducing the risk of spreading and bleeding. Additionally, using lower ink volumes per droplet can further enhance print quality by minimizing the amount of ink on the surface at any given time.
Curing Challenges
Curing is a critical step in UV printing, and it presents unique challenges when working with non-porous materials. UV inks cure through a photochemical reaction triggered by ultraviolet light. However, the curing process can be affected by several factors, including the substrate’s reflectivity, the intensity and wavelength of the UV light, and the ink’s chemical composition.
Non-porous materials often have high reflectivity, which can cause the UV light to scatter rather than penetrate the ink. This reduces the efficiency of the curing process and can lead to incomplete curing, resulting in tacky or undercured ink. To overcome this, printer manufacturers use UV lamps with specific wavelengths that are better absorbed by the ink, as well as reflective surfaces that direct the light more effectively.
Furthermore, the curing process must be tailored to the specific substrate and ink combination. Over-curing can cause the ink to become brittle and crack, while under-curing can result in poor durability and adhesion. Printers equipped with variable-power UV lamps and real-time curing monitoring systems can adjust the curing conditions dynamically, ensuring optimal results.
Color Consistency and Vibrancy
Achieving consistent and vibrant colors on non-porous materials is another technical hurdle. The reflective nature of these surfaces can cause colors to appear washed out or distorted. Additionally, the ink’s interaction with the substrate’s surface can alter its color properties.
To maintain color consistency, printer manufacturers employ color management systems that calibrate the printer and adjust the ink formulation in real-time. These systems use spectrophotometers to measure the color output and compare it to a reference standard, making adjustments as needed.
Moreover, using white ink as a base layer can significantly enhance color vibrancy on non-porous materials. White ink provides a reflective surface for the colored inks to adhere to, improving their appearance and making colors appear more saturated. This technique is particularly effective on transparent or dark-colored substrates.
Handling and Preparation of Non-Porous Materials
Finally, the handling and preparation of non-porous materials before printing present their own set of challenges. These materials are often heavier and more rigid than porous substrates, requiring specialized handling equipment to ensure they are positioned correctly on the printer bed.
Proper cleaning and pre-treatment of the surface are also essential. Any contaminants, such as dust, oil, or grease, can interfere with ink adhesion and cure. Cleaning the surface with appropriate solvents or abrasives can help remove these impurities, while pre-treatments like sanding or polishing can improve ink adhesion by creating a micro-rough surface for the ink to grip.
In some cases, the substrate may need to be heated or cooled to optimize the printing process. For example, heating a metal substrate can expand its pores slightly, making it more receptive to ink. Conversely, cooling a substrate can help control the curing process, preventing the ink from overheating and cracking.
Printing on non-porous materials with a UV flatbed printer is a technically challenging process that requires a deep understanding of both the printing technology and the substrate’s properties. Adhesion issues, ink spreading and bleeding, curing challenges, color consistency, and material handling are all critical factors that must be carefully managed to achieve high-quality prints.
By employing specialized inks, primers, and advanced printing techniques, as well as meticulous surface preparation and real-time monitoring, these challenges can be overcome. As UV flatbed printing technology continues to evolve, so too will our ability to print on a wider range of non-porous materials with greater ease and precision, opening up new possibilities for innovation and creativity in digital printing.