How to Troubleshoot Common Hardware Issues with UV Flatbed Printers
UV flatbed printers have revolutionized the printing industry by offering high-quality, durable prints on a wide range of materials. These printers utilize ultraviolet (UV) light to cure inks instantly, resulting in vibrant, scratch-resistant, and water-resistant prints. However, like any sophisticated piece of machinery, UV flatbed printers can encounter hardware issues that may disrupt their operation. This article aims to guide users through troubleshooting some of the most common hardware problems they might face with UV flatbed printers, ensuring minimal downtime and optimal performance.
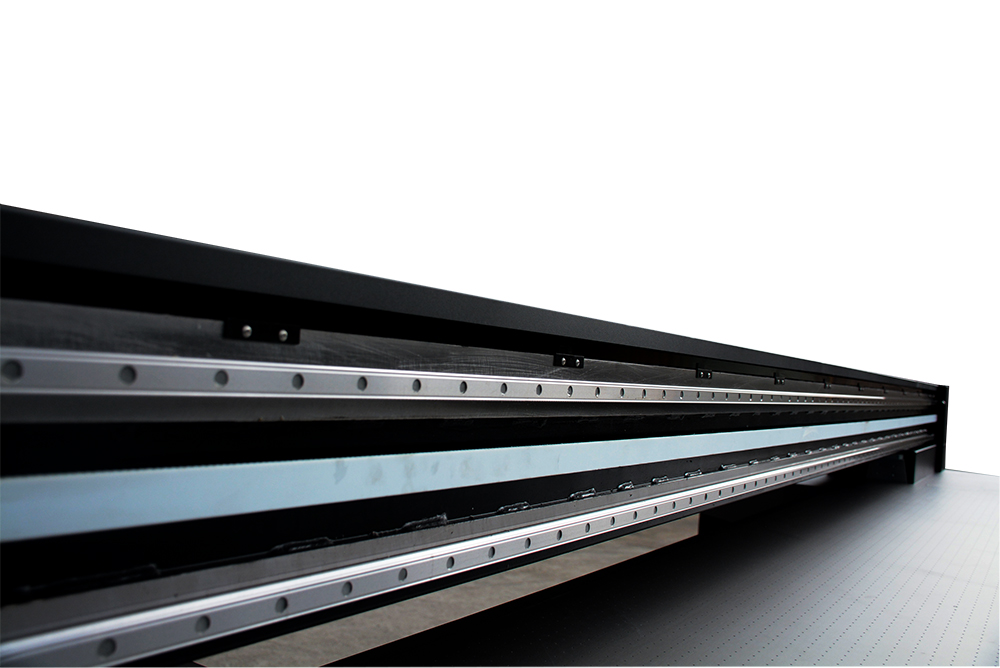
1. Understanding the Basics of UV Flatbed Printers
Before diving into troubleshooting, it’s essential to have a basic understanding of how UV flatbed printers work. These printers consist of several key components:
Print Heads: Responsible for depositing ink onto the media.
UV Lamps/LEDs: Cure the ink almost instantly after it’s deposited.
Ink Supply System: Ensures a steady flow of ink to the print heads.
Media Handling System: Manages the movement of the substrate under the print heads.
Control System: Manages the entire printing process, including ink ejection, lamp activation, and media movement.
2. Common Hardware Issues and Their Solutions
2.1 Print Head Clogging
Symptom: Inconsistent or missing print output, streaky lines.
Cause: Dry ink or debris in the nozzles.
Solution:
Perform a Nozzle Check: Most printers have a built-in function to test nozzle performance.
Run a Cleaning Cycle: Use the printer’s cleaning utility to flush out any clogged nozzles. This may use a significant amount of ink, so use it judiciously.
Manual Cleaning: If automatic cleaning fails, you may need to manually clean the print heads. This involves removing the print head assembly, soaking it in a cleaning solution recommended by the manufacturer, and gently flushing the nozzles with a syringe.
Preventive Measures: Regularly run maintenance cycles and avoid long periods of inactivity to prevent ink from drying in the nozzles.
2.2 UV Lamp/LED Failure
Symptom: Incomplete or slow curing of ink, resulting in smudging or poor print quality.
Cause: Faulty UV lamp or LED array, power supply issues.
Solution:
Inspect the Lamp/LEDs: Check for any visible damage or burnt-out sections.
Test the Power Supply: Ensure that the power supply to the UV system is stable and within the recommended range.
Replace the Lamp/LEDs: If damaged, replace the UV lamp or LED array following the manufacturer’s instructions.
Calibrate the Curing System: After replacement, calibrate the curing system to ensure even exposure and proper curing times.
2.3 Ink Supply Problems
Symptom: Ink not flowing, intermittent printing, or ink leakage.
Cause: Clogged ink lines, air bubbles in the ink system, or faulty ink cartridges/tanks.
Solution:
Check Ink Levels: Ensure that ink tanks or cartridges are not empty.
Prime the Ink System: Run a priming cycle to remove air bubbles and ensure ink flow.
Inspect Ink Lines and Connections: Check for kinks, leaks, or loose connections in the ink supply lines.
Replace Faulty Components: If a cartridge or tank is faulty, replace it with a new one.
2.4 Media Handling Issues
Symptom: Misalignment of prints, media jams, or feed errors.
Cause: Incorrect media settings, worn-out feed rollers, or debris on the media path.
Solution:
Check Media Settings: Ensure that the media type, thickness, and size are correctly set in the printer’s control panel.
Clean the Media Path: Remove any debris or dust from the feed rollers and media path using a lint-free cloth.
Inspect and Replace Rollers: Check the condition of the feed rollers. If they’re worn out or damaged, replace them.
Calibrate the Media Handling System: Follow the manufacturer’s instructions to calibrate the media feed system for accurate alignment and feeding.
2.5 Control System Malfunctions
Symptom: Printer not responding, error messages on the display, or unexpected behavior.
Cause: Software bugs, firmware issues, or hardware failures in the control board.
Solution:
Restart the Printer: Sometimes, a simple restart can resolve temporary software issues.
Update Firmware: Check the manufacturer’s website for any available firmware updates and follow the instructions to install them.
Check Connections: Ensure that all cables connecting the control board to other components are securely plugged in.
Contact Support: If the issue persists, it may be a more complex hardware problem. Contact the printer’s technical support for further assistance.
3. Preventive Maintenance Tips
To minimize the occurrence of hardware issues, regular preventive maintenance is crucial:
Schedule Regular Cleaning: Clean the printer’s exterior and interior, including print heads, media path, and UV lamps, according to the manufacturer’s guidelines.
Perform Routine Inspections: Regularly inspect all components for signs of wear or damage.
Use Genuine Parts and Supplies: Always use ink, media, and replacement parts recommended by the manufacturer to avoid compatibility issues.
Train Operators: Ensure that operators are familiar with the printer’s operation and basic troubleshooting steps.
UV flatbed printers are powerful tools that can significantly enhance the quality and versatility of your printing operations. However, like any machinery, they are susceptible to hardware issues that can disrupt their performance. By understanding the common problems and following the troubleshooting steps outlined in this article, you can quickly resolve many issues and keep your printer running smoothly. Remember, preventive maintenance is key to minimizing downtime and extending the life of your UV flatbed printer.