How to Troubleshoot Banding Issues on a UV Flatbed Printer
How to Troubleshoot Banding Issues on a UV Flatbed Printer
In the realm of digital printing, UV flatbed printers have revolutionized the way we print on a variety of substrates, offering versatility, precision, and durability. However, like any sophisticated machinery, they are not immune to issues that can affect print quality. One such common problem is banding, which refers to visible lines or stripes that appear across the printed image. These bands can detract from the overall aesthetic and professionalism of the print, making it crucial to address and resolve this issue promptly. This article delves into the various causes of banding in UV flatbed printers and provides comprehensive troubleshooting steps to help you achieve flawless prints.
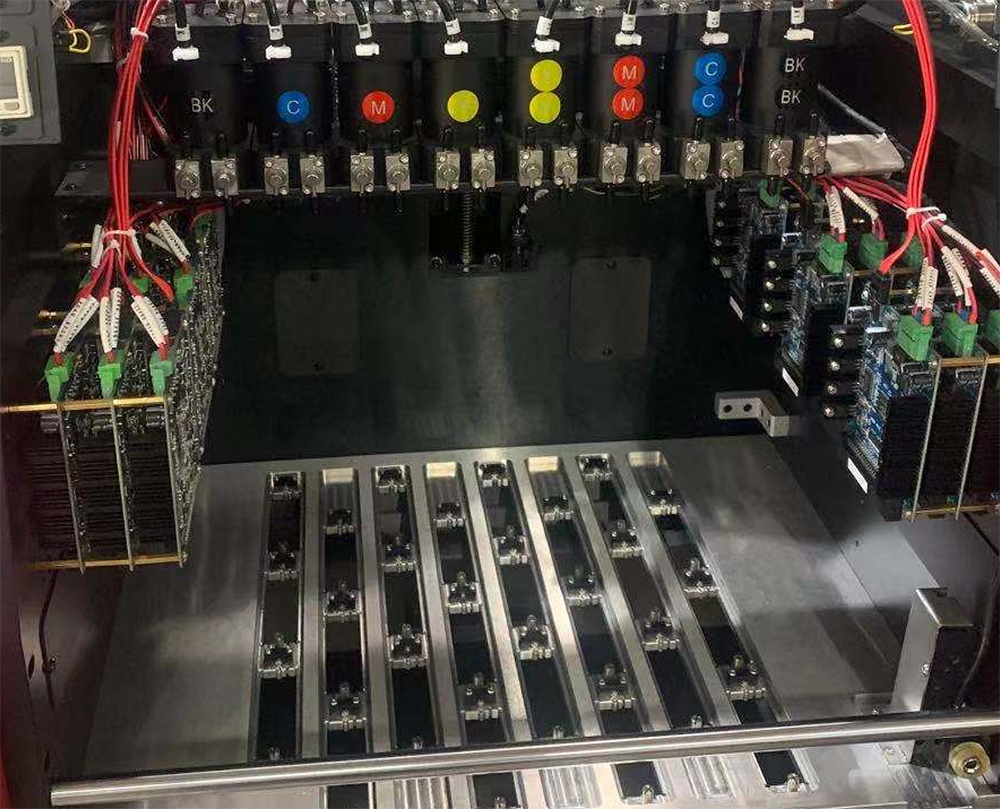
Understanding Banding
Banding typically occurs due to inconsistencies in the ink deposition process, resulting in areas where the ink coverage is not uniform. These inconsistencies can stem from mechanical, environmental, or operational factors. Before diving into the solutions, it’s essential to understand the potential root causes of banding:
Mechanical Issues:
Uneven Printhead Movement: If the printhead does not move smoothly across the substrate, it can lead to uneven ink distribution.
Worn or Damaged Printheads: Over time, printheads may wear out or get damaged, affecting their ability to eject ink consistently.
Dirty or Clogged Nozzles: Dust, debris, or dried ink can clog nozzles, disrupting the ink flow.
Ink and Material Handling:
Inconsistent Ink Viscosity: Variations in ink thickness can cause some areas to receive more or less ink than others.
Poor Ink Mixing: Improper mixing of inks can result in color inconsistencies and banding.
Substrate Quality: The texture, absorbency, and uniformity of the substrate can influence how ink is deposited.
Environmental Factors:
Temperature and Humidity: Fluctuations in temperature and humidity can affect the way ink dries and adheres to the substrate.
Airflow: Uncontrolled airflow around the printer can cause ink to dry unevenly or spread incorrectly.
Operational Settings:
Print Speed and Resolution: Higher print speeds may sacrifice some quality, while lower resolutions can make banding more noticeable.
Ink Drop Size: The size of the ink drops ejected by the printhead can impact the uniformity of the print.
Troubleshooting Steps
1. Inspect and Clean the Printhead
Regular Maintenance: Schedule regular cleanings to prevent nozzle clogs and ensure optimal printhead performance.
Manual Cleaning: Use a cleaning solution and lint-free cloth to gently wipe the printhead. Follow the manufacturer’s guidelines to avoid damaging the delicate components.
Automated Cleaning Cycles: Utilize the printer’s built-in cleaning functions to clear any minor clogs or debris.
2. Check Printhead Alignment
Calibration: Run a printhead alignment test and adjust as necessary. Most UV flatbed printers have built-in tools for this purpose.
Mechanical Inspection: Ensure that the printhead carriage moves smoothly without any obstructions or misalignment.
3. Monitor Ink Quality and Handling
Ink Viscosity: Use a viscometer to check the ink’s viscosity regularly and adjust it according to the manufacturer’s specifications.
Ink Storage: Store inks in a controlled environment to avoid temperature fluctuations and contamination.
Mixing: Follow proper mixing procedures to ensure consistent color and quality throughout the ink supply.
4. Optimize Environmental Conditions
Climate Control: Maintain a stable temperature and humidity level in the printing area. Ideally, the environment should be between 20-25°C (68-77°F) with relative humidity around 40-60%.
Airflow Management: Minimize drafts and ensure that the printing area is shielded from direct airflow, which can disrupt ink deposition.
5. Adjust Print Settings
Print Speed: Reduce the print speed to allow for better ink adhesion and more controlled ink deposition.
Resolution: Increase the print resolution to ensure smoother transitions between colors and reduce the visibility of banding.
Ink Drop Size: Adjust the ink drop size settings to find the optimal balance between print speed and quality. Smaller drops can result in smoother prints but may require more passes to achieve the desired color saturation.
6. Evaluate the Substrate
Substrate Choice: Test different substrates to see which ones produce the best results with your printer and ink combination.
Preparation: Ensure the substrate is clean, dry, and properly prepared for printing. Some materials may require pre-treatment to improve ink adhesion.
7. Update Firmware and Software
Manufacturer Updates: Regularly check for and install firmware and software updates provided by the printer manufacturer. These updates often include bug fixes and performance improvements that can address banding issues.
Driver Updates: Ensure that your printer drivers are up to date to maintain compatibility with your operating system and software.
8. Test and Experiment
Print Test Patterns: Print test patterns with varying settings to identify the optimal configuration for your specific needs.
Keep a Log: Maintain a detailed log of your prints, including settings, substrates, and any issues encountered. This can help you identify patterns and pinpoint the cause of banding more quickly in the future.
Advanced Troubleshooting
If basic troubleshooting steps fail to resolve the banding issue, consider the following advanced techniques:
Printhead Replacement: If the printhead is significantly worn or damaged, it may need to be replaced. Consult the manufacturer for guidance on when and how to replace the printhead.
Professional Service: In some cases, banding issues may be due to more complex mechanical or electrical problems that require the expertise of a professional technician. Don’t hesitate to contact the printer’s manufacturer or a certified service provider for assistance.
Upgrade Components: Consider upgrading key components such as the printhead, ink system, or control board to improve print quality and reliability.
Banding issues in UV flatbed printers can be frustrating, but with a systematic approach to troubleshooting, they can be effectively addressed. By regularly maintaining your printer, monitoring ink quality, optimizing environmental conditions, and adjusting print settings, you can significantly reduce the occurrence of banding and achieve high-quality prints. Remember, the key to successful troubleshooting is patience, attention to detail, and a willingness to experiment with different solutions. With these strategies in place, you’ll be well-equipped to tackle banding issues and ensure that your UV flatbed printer produces stunning results every time.