How to Print on Flexible Materials with UV Flatbed Printers
UV flatbed printers have revolutionized the printing industry by enabling high-quality, versatile output on a wide range of materials, including rigid substrates like glass, metal, and wood. However, their capabilities extend far beyond rigid surfaces—they can also print on flexible materials, opening doors to creative applications in packaging, textiles, signage, and more. This guide explores the techniques, considerations, and best practices for achieving professional results when printing on flexible materials using UV flatbed printers.
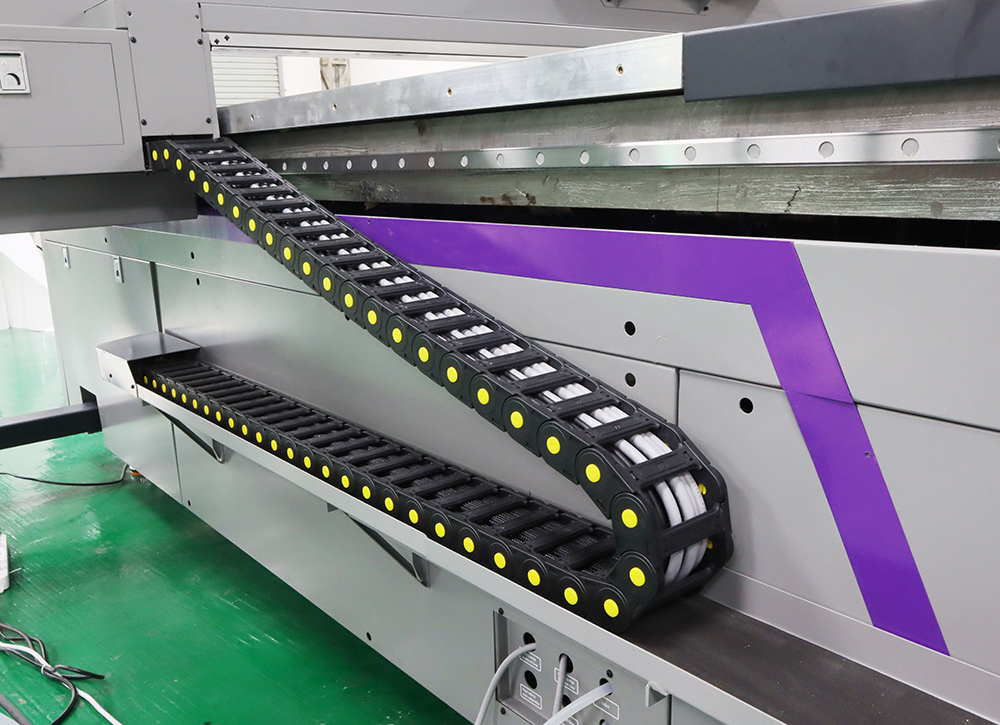
Understanding UV Flatbed Printing on Flexible Substrates
UV flatbed printers use ultraviolet light to cure ink instantly upon contact with the material. This process ensures vibrant colors, durability, and resistance to fading. When printing on flexible materials, the challenge lies in accommodating the material’s tendency to bend, stretch, or curl. Unlike rigid substrates, flexible materials require adjustments to printer settings, material handling, and finishing techniques to ensure adhesion and longevity.
Key advantages of UV printing on flexible materials include:
Versatility: Works with fabrics, vinyl, leather, and synthetic films.
Speed: Instant curing reduces production time.
Durability: UV-cured ink resists scratches, water, and UV exposure.
Preparing Flexible Materials for Printing
Before loading flexible materials into a UV flatbed printer, proper preparation is essential to avoid issues like ink smudging, poor adhesion, or material warping.
Surface Cleaning: Flexible materials often accumulate dust, oils, or residues. Wipe the surface with a lint-free cloth dampened with isopropyl alcohol or a mild cleaner. Ensure the material is completely dry before printing.
Priming (If Needed): Some flexible substrates, such as certain plastics or treated fabrics, may require a primer to improve ink adhesion. Apply a thin, even layer of primer and allow it to dry per the manufacturer’s instructions.
Static Elimination: Static electricity can cause ink to misalign or attract dust. Use an anti-static spray or ionizing bar to neutralize static before printing.
Material Tensioning: For roll-to-roll flexible materials (if your printer supports it), ensure even tension to prevent wrinkles or misalignment. Clamp or tape the edges securely to the printer bed.
Optimizing Printer Settings for Flexible Substrates
UV flatbed printers offer adjustable settings to accommodate different materials. Here’s how to tweak them for flexible substrates:
Ink Drop Size: Use smaller drop sizes for detailed prints on thin or delicate materials to prevent ink pooling.
Curing Intensity: Reduce UV lamp power slightly to avoid overheating the material, which could cause warping or shrinkage.
Print Height Adjustment: Raise the print head slightly to prevent scratching the material’s surface, especially for textured or uneven flexible substrates.
Pass Count: Increase the number of passes for better opacity on transparent or porous materials.
Test prints are crucial. Print a small sample first to check for adhesion, color accuracy, and material distortion.
Handling Common Challenges
Printing on flexible materials isn’t without hurdles. Here’s how to troubleshoot common issues:
Ink Adhesion Problems:
Cause: Low-surface-energy materials (e.g., polypropylene) may repel ink.
Solution: Use a primer or corona treatment to increase surface energy.
Material Curling or Warping:
Cause: Excessive heat from UV lamps or uneven material tension.
Solution: Reduce lamp intensity, increase airflow, or use a heat-resistant backing.
Color Inconsistency:
Cause: Ink absorption varies across material types.
Solution: Create custom color profiles for each flexible substrate.
Static Cling:
Cause: Dry environments or material friction.
Solution: Increase humidity in the printing area or use anti-static tools.
Post-Printing Finishing Techniques
After printing, finishing steps enhance durability and aesthetics:
Lamination: Apply a clear or matte laminate film to protect the print from scratches, UV rays, or moisture.
Cutting and Die-Cutting: Use a plotter or laser cutter to trim flexible materials into custom shapes. Ensure the material is securely held during cutting to prevent shifting.
Heat Pressing (for Textiles): For fabric prints, a heat press can improve ink adhesion and washability. Follow the ink manufacturer’s guidelines for temperature and time.
Storage: Roll printed flexible materials (print side out) to avoid creasing. Store in a cool, dry place away from direct sunlight.
Applications and Creative Ideas
UV flatbed printing on flexible materials unlocks endless possibilities:
Custom Packaging: Print vibrant designs on flexible films for food wraps, cosmetic pouches, or e-commerce mailers.
Retail Signage: Create lightweight, durable banners, backdrops, or window graphics using vinyl or fabric.
Textile Decor: Print on synthetic fabrics for apparel, upholstery, or soft signage.
Automotive Graphics: Apply UV-printed decals to vehicle wraps or interior trim.
Promotional Items: Customize reusable bags, lanyards, or inflatable displays.
Sustainability Considerations
As eco-consciousness grows, consider sustainable practices:
Ink Choices: Opt for UV-curable inks with low volatile organic compounds (VOCs).
Material Recycling: Use recyclable or biodegradable flexible substrates when possible.
Waste Reduction: Minimize material scraps through precise nesting and efficient cutting.
Conclusion
Printing on flexible materials with UV flatbed printers combines technical precision with creative freedom. By understanding material properties, optimizing printer settings, and mastering finishing techniques, businesses can produce high-quality, durable prints for diverse applications. Whether for packaging, signage, or textiles, UV flatbed printing offers a versatile solution to meet evolving market demands. Experiment, test, and refine your approach to unlock the full potential of this innovative technology.