How to Choose the Right Finishing Options for UV-Printed Materials
How to Choose the Right Finishing Options for UV-Printed Materials
Ultraviolet (UV) printing has revolutionized the printing industry with its ability to produce high-quality, durable, and vibrant prints on a wide range of materials. From signage to packaging, UV printing offers versatility and efficiency that traditional printing methods cannot match. However, the process does not end with just the printing; finishing options play a crucial role in enhancing the final appearance, durability, and functionality of UV-printed materials. Choosing the right finishing options can significantly impact the overall aesthetic and performance of the printed product. This comprehensive guide explores the various finishing options available for UV-printed materials and provides insights into selecting the most suitable ones for different applications.
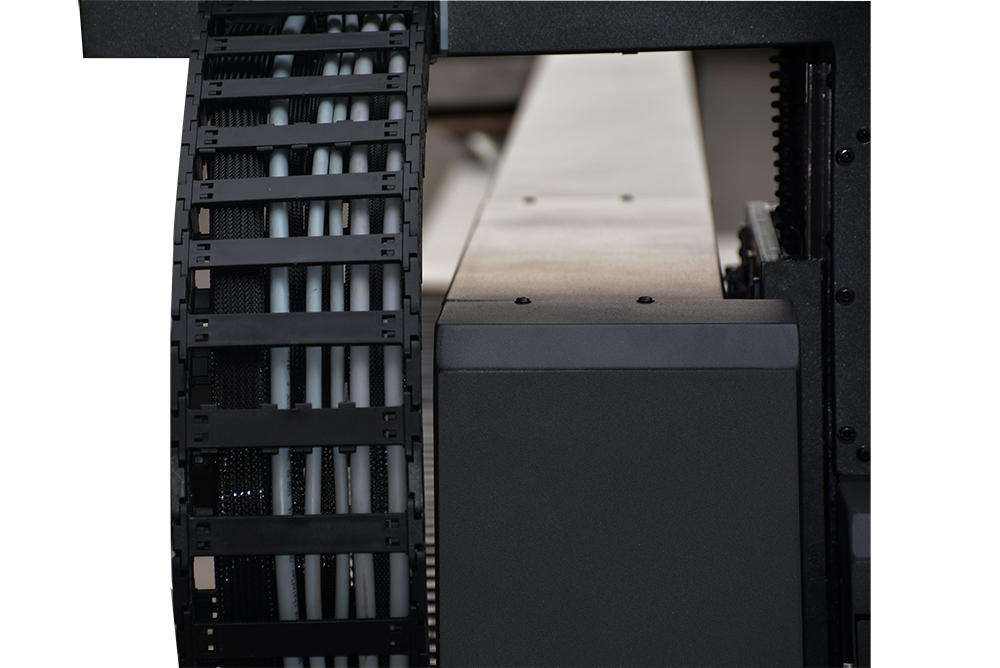
Understanding UV Printing
Before delving into finishing options, it is essential to grasp the basics of UV printing. UV printing utilizes ultraviolet light to cure or dry inks almost instantly after they are applied to a substrate. This method allows for precise control over the ink, resulting in sharp images, vibrant colors, and the ability to print on various materials, including plastics, metals, glass, and more.
The rapid curing process of UV inks offers several advantages:
Fast Turnaround Times: Quick drying enables higher productivity.
Enhanced Durability: UV-cured inks are more resistant to fading, scratching, and chemicals.
Versatility: Can print on a wide range of substrates with varying textures and thicknesses.
Environmental Benefits: UV printing often uses fewer volatile organic compounds (VOCs) compared to traditional printing methods.
Importance of Finishing Options
Finishing options are the final touches that can elevate the quality and appeal of UV-printed materials. They not only enhance the visual aesthetics but also contribute to the durability and functionality of the prints. The choice of finishing depends on several factors, including the intended use of the material, the desired look, and the budget.
Common Finishing Options for UV-Printed Materials
1. Lamination
Lamination involves applying a thin, transparent film to the printed surface. It is one of the most popular finishing options due to its ability to provide a protective barrier while enhancing the appearance.
Gloss Lamination: Gives a shiny, reflective finish, ideal for creating a high-end, polished look. It is commonly used for marketing materials, brochures, and presentations.
Matte Lamination: Offers a non-glossy, smooth finish that reduces glare and fingerprints. It is preferred for reading materials like books and magazines.
Textured Lamination: Adds a tactile element to the print, providing both visual and sensory appeal. Textured laminates can mimic surfaces like leather, wood, or fabric.
2. Varnishing
Varnish is a clear, protective coating applied over the printed area. It can be used selectively (spot varnish) or over the entire surface (flood varnish).
Gloss Varnish: Provides a shiny finish similar to gloss lamination but with a thinner application. It highlights specific areas of the print, drawing attention to key elements.
Matte Varnish: Offers a subtle, non-reflective finish that can add depth and softness to the printed materials.
UV Varnish: Cures instantly under UV light, offering excellent durability and resistance to wear and tear.
3. Embossing and Debossing
Embossing creates a raised relief on the printed surface, while debossing (also known as counter-embossing) creates a depressed or recessed area.
Blind Embossing/Debossing: Involves creating raised or recessed areas without applying any ink or color, adding tactile elements to the print.
Registered Embossing/Debossing: Aligns the embossed or debossed areas with specific printed elements, enhancing visual and tactile engagement.
4. Foil Stamping
Foil stamping involves applying a thin layer of metallic or colored foil to the printed surface using heat and pressure. It adds a touch of elegance and luxury, often used for branding, invitations, and premium packaging.
Gold/Silver Foil: Classic options that add a metallic shine.
Colored Foil: Available in various hues to match brand colors or create unique effects.
Holographic Foil: Offers a dynamic, shimmering effect that changes with the light.
5. Die Cutting
Die cutting involves using a sharp blade or laser to cut shapes or patterns into the printed material. It is commonly used for creating custom shapes, labels, and packaging.
Standard Die Cutting: Uses pre-made dies to cut uniform shapes.
Custom Die Cutting: Allows for intricate and unique shapes tailored to specific designs.
6. UV Coating
Similar to varnish, UV coating is a clear, protective layer that is cured under UV light. It offers excellent durability and can be applied in various finishes.
Gloss UV Coating: Provides a high-gloss, reflective finish.
Matte UV Coating: Offers a smooth, non-reflective surface.
Textured UV Coating: Adds a tactile element with various textures.
Factors to Consider When Choosing Finishing Options
Selecting the right finishing options for UV-printed materials requires careful consideration of several factors:
1. Intended Use
The primary function of the printed material will significantly influence the choice of finishing. For example, outdoor signage will require durable, weather-resistant finishes, while marketing brochures may prioritize visual appeal and tactile engagement.
2. Substrate Material
The type of material being printed on plays a crucial role. Some finishes may adhere better to certain substrates. For instance, certain laminations may not be suitable for flexible materials like fabric or certain types of plastics.
3. Design Aesthetics
The overall design and brand identity should guide the selection of finishing options. A high-end, luxurious brand may opt for gold foil stamping and gloss lamination, while a more eco-conscious brand may choose matte finishes and UV coatings that highlight the natural texture of the substrate.
4. Budget Considerations
Cost is always a factor. Some finishing options, like foil stamping and custom die cutting, can be more expensive than others. It’s essential to balance cost with the desired outcome and the value the finishing will add to the final product.
5. Durability and Lifespan
Consider how long the printed material needs to last and the conditions it will be exposed to. High-traffic areas or outdoor applications may require more durable finishes to withstand wear and tear.
6. Environmental Impact
With growing environmental concerns, it’s important to consider the sustainability of finishing options. Opt for materials and processes that have a lower environmental impact, such as using recyclable laminates or water-based UV coatings.
Conclusion
Choosing the right finishing options for UV-printed materials is a blend of art and science. It requires a deep understanding of the available options, their aesthetic and functional benefits, and how they align with the specific needs of the project. By carefully considering factors like intended use, substrate material, design aesthetics, budget, durability, and environmental impact, you can enhance the overall quality and appeal of UV-printed materials.
Finishing options are not just afterthoughts; they are integral to the printing process, contributing significantly to the final outcome. Whether it’s the sleek sophistication of gloss lamination, the tactile engagement of embossing, or the eye-catching allure of foil stamping, each finishing option brings its unique value to the table.
As technology continues to evolve, so will the finishing options available for UV-printed materials. Staying informed about the latest trends and innovations in the industry will enable you to make more informed decisions, ensuring that your printed materials stand out in a competitive market.
In summary, the right finishing options can elevate UV-printed materials from ordinary to extraordinary. They add depth, texture, and durability, making the prints more engaging and long-lasting. By carefully evaluating your needs and exploring the wide range of finishing options available, you can create printed materials that not only look stunning but also perform exceptionally well in their intended applications.