How to Achieve High-Gloss Finishes with a UV Flatbed Printer?
How to Achieve High-Gloss Finishes with a UV Flatbed Printer?
In the realm of digital printing, achieving a high-gloss finish is often a coveted goal for businesses seeking to produce visually stunning and professional-grade products. UV flatbed printers have emerged as a popular choice for achieving such finishes due to their ability to print directly onto various materials with exceptional detail and vibrant colors. This article delves into the intricacies of how to effectively achieve high-gloss finishes using a UV flatbed printer, exploring key considerations, techniques, and best practices.
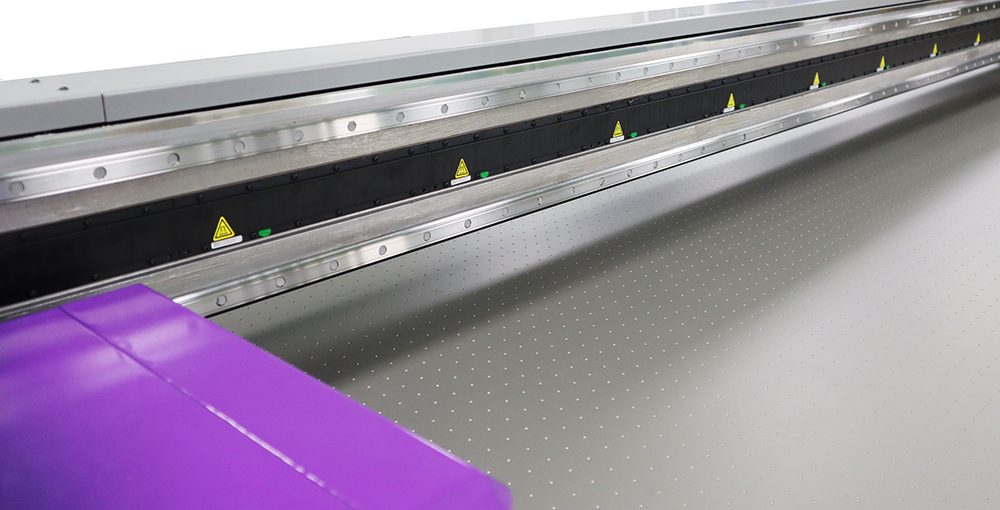
Understanding UV Flatbed Printers
UV flatbed printers utilize ultraviolet (UV) light to instantly cure ink as it is applied to the substrate. This technology allows for precise control over ink deposition, resulting in sharp images and vibrant colors. The UV curing process also enables printing on a wide range of materials, including plastics, glass, metal, and even some textiles, without the need for pre-treatment or priming.
One of the significant advantages of UV flatbed printers is their ability to produce high-gloss finishes. The instant curing of the ink prevents smudging or bleeding, ensuring a smooth and glossy surface. However, achieving the desired gloss level requires careful consideration of several factors, including ink selection, substrate preparation, print settings, and post-print handling.
Ink Selection for High-Gloss Finishes
The choice of ink plays a pivotal role in achieving a high-gloss finish. UV-curable inks specifically designed for flatbed printers offer superior gloss levels compared to traditional solvent or aqueous inks. These inks contain resins that, when cured under UV light, form a hard, smooth surface. Look for inks that are specifically marketed for their gloss properties and are compatible with your printer model.
Consider the ink’s viscosity and flow characteristics as well. Inks with lower viscosity tend to spread more evenly, reducing the risk of ink piling or uneven gloss. Additionally, inks with good flow properties will self-level during the curing process, contributing to a smoother, more glossy finish.
Substrate Preparation
Proper substrate preparation is crucial for achieving a high-gloss finish. Ensure that the printing surface is clean, dry, and free from any dust, oils, or contaminants that could interfere with ink adhesion. For porous materials, consider applying a thin coat of primer to improve ink adhesion and enhance gloss uniformity.
It’s also important to consider the substrate’s ability to reflect light. Materials with a naturally smooth surface, such as polished metals or glass, will inherently provide a better gloss finish than rough or textured surfaces. If working with a textured substrate, experiment with thinner ink layers or consider using a clear coat to smooth out the surface and enhance gloss.
Print Settings and Techniques
Achieving a high-gloss finish requires careful adjustment of print settings. Start by selecting the appropriate print mode in your printer’s software, often labeled as “high gloss” or “gloss optimized.” These modes adjust ink deposition and curing parameters to maximize gloss.
Ink coverage and layering are also critical. While heavy ink deposition can enhance color saturation, it can also result in a dull, uneven finish if not properly controlled. Experiment with ink density and layering to find the optimal balance between color intensity and gloss. In some cases, applying multiple thin layers of ink can yield a smoother, more glossy result than a single thick layer.
Curing temperature and duration play a significant role in gloss development. Higher curing temperatures can accelerate the ink’s curing process, leading to a harder, more glossy surface. However, excessive heat can also cause ink to crack or yellow. Consult your printer’s manufacturer guidelines for recommended curing temperatures and durations.
Post-Print Handling
Post-print handling can significantly impact the final gloss level of your prints. Allow prints to cool completely before handling to prevent any heat-related issues, such as ink softening or adhesion problems. Avoid touching the printed surface unnecessarily, as fingerprints or oils from your skin can mar the gloss finish.
For applications requiring additional protection or gloss enhancement, consider applying a UV-curable clear coat. This can fill in any minor imperfections in the ink layer, resulting in a smoother, more uniform gloss. Be sure to follow the clear coat manufacturer’s instructions for proper application and curing.
Quality Control and Testing
Achieving consistent high-gloss finishes requires ongoing quality control and testing. Regularly inspect your prints for gloss uniformity, ink adhesion, and overall appearance. Use gloss meters to measure gloss levels objectively and compare results across different substrates and ink formulations.
Keep detailed records of your print settings, ink usage, and substrate preparations. This documentation will help you identify any variables that may be affecting gloss consistency and make adjustments accordingly.
Conclusion
Achieving high-gloss finishes with a UV flatbed printer is a multifaceted process that requires careful consideration of ink selection, substrate preparation, print settings, and post-print handling. By understanding the intricacies of UV printing technology and experimenting with different techniques and materials, you can unlock the full potential of your UV flatbed printer to produce stunning, high-gloss prints that meet or exceed your customers’ expectations. Remember, achieving consistent high-gloss finishes is an ongoing process of learning, testing, and refinement. With practice and attention to detail, you can master the art of high-gloss UV printing and elevate your printing projects to new levels of visual impact.