How Does UV Curing Affect Print Quality in UV Flatbed Printers
In the realm of digital printing, UV flatbed printers have emerged as a game-changer, offering unprecedented versatility and efficiency. These printers leverage UV curing technology to achieve high-quality prints on a wide range of materials, from soft fabrics to hard surfaces like glass, ceramics, and metals. Understanding how UV curing impacts print quality is crucial for maximizing the potential of these advanced machines. This article delves into the intricacies of UV curing and its role in enhancing print quality in UV flatbed printers.
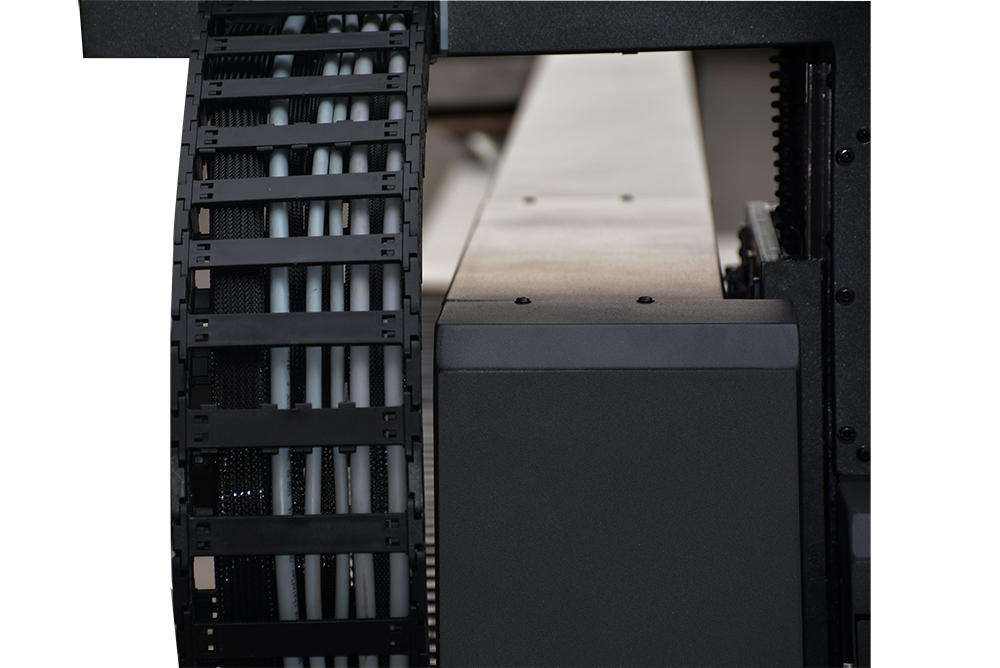
The Fundamentals of UV Curing
UV curing, also known as ultraviolet curing, is a process that utilizes ultraviolet light to initiate a chemical reaction, leading to the polymerization of monomers or oligomers into polymers. This technology has been around since the late 19th century, with practical applications starting in the 1940s. UV curing offers several advantages over conventional drying methods, such as rapid curing speeds, low energy consumption, and the ability to cure coatings and inks without the use of solvents.
In the context of UV flatbed printers, UV curing is employed to instantly cure UV-curable inks after they are jetted onto the print surface. These inks contain photoinitiators that absorb UV light and convert it into chemical energy, triggering the polymerization of the ink components. This results in the formation of a solid, durable print layer that adheres strongly to the substrate.
The Components of UV Curing in UV Flatbed Printers
UV Light Source
The UV light source is the heart of the UV curing process in UV flatbed printers. Common types of UV lamps include mercury vapor lamps, LED UV lamps, and excimer lamps. Each type has its unique characteristics in terms of wavelength, intensity, and lifetime.
Mercury Vapor Lamps: These lamps produce a broad spectrum of UV light, making them suitable for a wide range of UV-curable inks. However, they have a relatively short lifetime and generate significant heat.
LED UV Lamps: LED UV lamps offer a narrower wavelength range, higher energy efficiency, and longer lifetime compared to mercury vapor lamps. They are becoming increasingly popular due to their environmental benefits and reduced operational costs.
Excimer Lamps: These lamps produce high-intensity UV light at specific wavelengths, making them ideal for applications requiring precision curing. However, they are more expensive and have a shorter lifetime.
UV-Curable Inks
UV-curable inks are formulated to respond to UV light by undergoing polymerization. They typically consist of oligomers, monomers, photoinitiators, and additives such as pigments and flow modifiers. The photoinitiators play a crucial role in the curing process by absorbing UV light and generating free radicals or ions that initiate the polymerization of the ink components.
The Impact of UV Curing on Print Quality
Curing Speed and Efficiency
One of the most significant advantages of UV curing in UV flatbed printers is its rapid curing speed. Traditional drying methods, such as air drying or heat curing, can take minutes or even hours to achieve complete drying. In contrast, UV curing can complete the curing process in seconds, significantly increasing production efficiency.
The curing speed is influenced by several factors, including the intensity of the UV light source, the type and formulation of the UV-curable ink, and the distance between the UV light source and the print surface. Optimizing these parameters ensures that the ink is fully cured without overexposure, which can lead to embrittlement or discoloration of the print.
Adhesion and Durability
UV curing enhances the adhesion and durability of prints on various substrates. The strong bond formed between the cured ink and the substrate ensures that the print remains intact and resistant to scratching, peeling, and fading over time. This is particularly important in applications where prints are exposed to harsh environments or require high durability, such as in signage, packaging, and industrial labeling.
The adhesion and durability of prints are influenced by the surface energy of the substrate, the type of UV-curable ink used, and the curing conditions. Proper surface preparation, such as cleaning and priming, can further improve the adhesion of prints on difficult-to-bond substrates.
Print Resolution and Detail
UV curing plays an indirect but crucial role in the print resolution and detail achievable with UV flatbed printers. By enabling the rapid curing of UV-curable inks, UV curing allows for higher print speeds and reduced downtime between prints. This, in turn, enables printers to produce finer details and higher resolutions without compromising on production efficiency.
The print resolution and detail are also influenced by the type and quality of the print head, the ink droplet size, and the ink formulation. UV-curable inks formulated with smaller particle sizes and higher pigment concentrations can produce prints with sharper edges and more vibrant colors.
Color Accuracy and Consistency
UV curing can affect color accuracy and consistency in UV flatbed printers. The curing process can lead to slight changes in the color properties of UV-curable inks, such as shifts in hue, saturation, and brightness. These changes can be minimized by carefully selecting inks formulated for consistent color performance under UV light and optimizing the curing conditions.
Color management systems and profiling tools can also be used to ensure color accuracy and consistency across different prints and substrates. These tools allow printer operators to adjust the color output to match specific color standards or customer requirements.
Challenges and Considerations in UV Curing
Despite its numerous advantages, UV curing in UV flatbed printers is not without challenges. Here are some considerations for printer operators to keep in mind:
Heat Generation
UV light sources, especially mercury vapor lamps, generate significant heat during the curing process. This heat can cause thermal expansion of the print head and substrate, leading to misregistration and print distortions. To mitigate this issue, UV flatbed printers are equipped with cooling systems that maintain the temperature within acceptable limits.
UV Light Exposure
Overexposure to UV light can lead to embrittlement or discoloration of the print. Conversely, underexposure can result in incomplete curing, affecting the adhesion and durability of the print. Proper calibration of the UV light source and the use of UV-curable inks formulated for the specific UV light spectrum are crucial for achieving optimal curing results.
Ink Selection and Compatibility
Not all UV-curable inks are compatible with all UV light sources and substrates. Printer operators must select inks that are compatible with their printer’s UV light source and the specific substrates they intend to print on. Additionally, the viscosity, surface tension, and cure speed of the ink must be tailored to the print head and curing conditions to ensure optimal print quality.
Future Trends and Innovations in UV Curing
The field of UV curing in UV flatbed printers is constantly evolving. Here are some future trends and innovations to look out for:
Advanced UV Light Sources
The development of more efficient and precise UV light sources, such as high-power LED UV lamps and pulsed UV lasers, will enable faster curing speeds, lower energy consumption, and improved color consistency. These advanced light sources will also allow for more flexible and customizable curing profiles to meet the specific needs of different applications.
Sustainable UV-Curable Inks
The increasing demand for sustainable printing solutions will drive the development of UV-curable inks with lower environmental impact. This includes inks formulated with renewable resources, reduced volatile organic compound (VOC) emissions, and enhanced biodegradability.
Intelligent Curing Systems
The integration of artificial intelligence (AI) and machine learning (ML) technologies into UV curing systems will enable more precise and adaptive curing profiles. These systems will be able to monitor and adjust the curing conditions in real-time based on the specific characteristics of the ink, substrate, and print job, ensuring optimal print quality and efficiency.
Multi-functional UV Curing
The development of multi-functional UV curing systems that can cure multiple ink layers or different types of inks simultaneously will enhance the versatility and productivity of UV flatbed printers. These systems will enable printers to produce complex, multi-layered prints with a wider range of effects and finishes.
UV curing plays a pivotal role in enhancing print quality in UV flatbed printers. By enabling the rapid curing of UV-curable inks, UV curing increases production efficiency, improves adhesion and durability, and enhances print resolution and detail. However, printer operators must be aware of the challenges associated with UV curing, such as heat generation, UV light exposure, and ink compatibility. As the field of UV curing continues to evolve, we can expect to see more advanced UV light sources, sustainable UV-curable inks, intelligent curing systems, and multi-functional UV curing solutions that will further elevate the capabilities of UV flatbed printers.