How Does UV Curing Affect Print Durability?
How Does UV Curing Affect Print Durability?
In the realm of printing technology, achieving optimal print durability is paramount for ensuring that prints retain their quality and integrity over time. One crucial factor that significantly influences this outcome is the curing process, particularly UV curing. This method has gained widespread popularity across various printing applications due to its efficiency and effectiveness in enhancing print properties. This article delves into the intricacies of UV curing and its profound impact on print durability, exploring the mechanisms at play, the benefits it offers, and the considerations involved in achieving desired results.
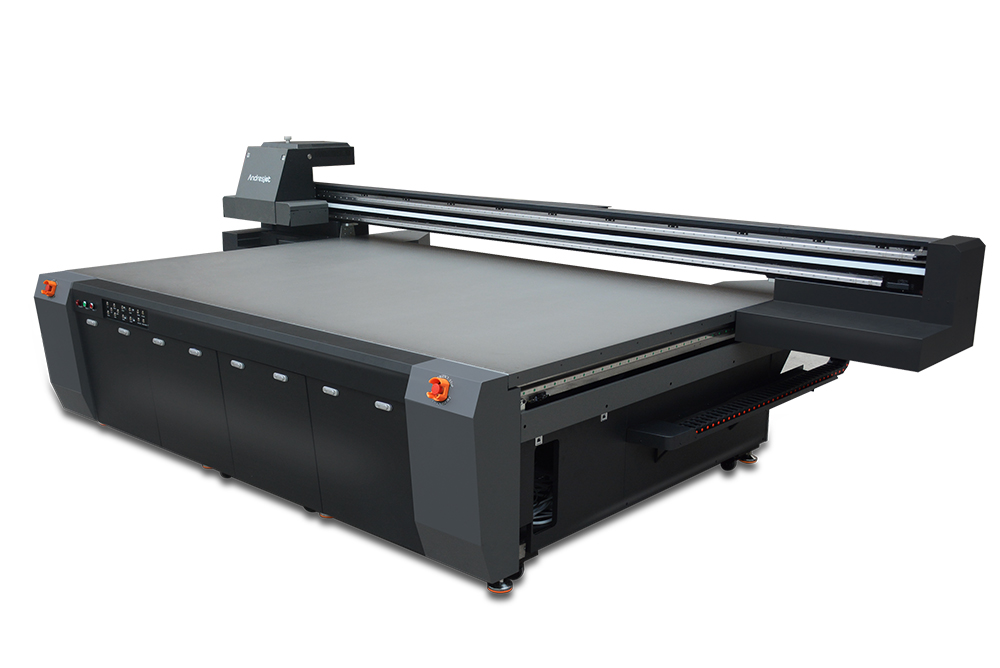
Understanding UV Curing
UV curing, also known as ultraviolet curing, is a process where high-energy ultraviolet light is used to instantly cure or harden inks, adhesives, and other coatings. This technology leverages the power of UV radiation to initiate a chemical reaction within these materials, causing them to solidify rapidly. The process typically involves applying a UV-curable material to a substrate and then exposing it to UV light, usually in the range of 200 to 400 nanometers.
The UV light interacts with photoinitiators present in the curable material, which absorb the UV energy and convert it into chemical energy. This energy triggers a chain reaction of polymerization, where individual molecules link together to form larger, more stable polymer chains. As a result, the material transitions from a liquid or gel state to a solid, fully cured state in a matter of seconds.
Mechanisms Influencing Print Durability
Print durability refers to the ability of a printed material to withstand various environmental and mechanical stresses without significant degradation in quality. Several mechanisms contribute to the enhancement of print durability through UV curing:
Cross-Linking: During UV curing, the formation of cross-links between polymer chains significantly increases the material’s molecular weight and density. This cross-linked structure provides enhanced resistance to chemicals, abrasion, and solvent attack, thereby improving durability.
Instant Curing: The rapid curing time of UV-curable materials minimizes the risk of contamination and allows for better control over the final print quality. This quick solidification also reduces the chances of shrinkage or distortion, ensuring dimensional stability.
Improved Adhesion: UV curing can promote stronger adhesion between the ink or coating and the substrate. This bond strength is crucial for preventing delamination, cracking, or peeling, especially under stress conditions.
Hardness and Scratch Resistance: The cured material often exhibits increased hardness and scratch resistance, making it more resilient to everyday wear and tear.
Weatherability: UV-cured prints typically show better resistance to UV light, moisture, and temperature extremes, which are major contributors to print degradation over time.
Benefits of UV Curing for Print Durability
The advantages of UV curing in enhancing print durability are manifold:
Enhanced Lifespan: Prints cured with UV technology often have a longer lifespan, maintaining their vibrant colors and clear details even after prolonged exposure to harsh conditions.
Cost-Effectiveness: The fast curing process reduces labor costs and increases production efficiency, making it an economically viable option for high-volume printing.
Environmental Benefits: UV curing is a solvent-free process, emitting no volatile organic compounds (VOCs). This makes it more environmentally friendly compared to traditional solvent-based curing methods.
Versatility: UV-curable materials can be formulated to meet a wide range of application needs, from flexible packaging to rigid signage, offering versatility in printing on various substrates.
Improved Aesthetics: The high-quality finish achieved through UV curing enhances the visual appeal of prints, making them more attractive and professional.
Considerations for Optimal UV Curing
While UV curing offers numerous benefits, achieving optimal results requires careful consideration of several factors:
UV Light Source: The type and intensity of the UV light source play a critical role. Different UV-curable materials require specific wavelengths and energy levels for effective curing. LED-based UV systems, for instance, offer energy efficiency and precise control over curing conditions.
Curing Time and Distance: The duration of exposure and the distance between the UV light source and the substrate must be precisely controlled. Overexposure can lead to overcuring, causing the material to become brittle, while underexposure results in incomplete curing and reduced durability.
Substrate Compatibility: Not all substrates are compatible with UV-curable materials. It is essential to ensure that the substrate can withstand the curing process without warping, melting, or otherwise being damaged.
Ink and Coating Formulation: The composition of the UV-curable ink or coating significantly impacts its curing behavior and ultimate durability. Formulations should be tailored to the specific application requirements, taking into account factors such as desired hardness, flexibility, and resistance to particular environmental conditions.
Post-Curing Processes: In some cases, additional post-curing steps, such as thermal treatment, may be necessary to further enhance the durability of the print. These steps can help to complete the cross-linking process and eliminate any residual volatiles.
Real-World Applications
UV curing is extensively used in various printing applications where durability is a key consideration:
Graphic Arts: UV-cured inks are commonly used in digital printing, screen printing, and offset printing for producing high-quality graphics that resist fading and wear.
Packaging: In the packaging industry, UV curing ensures that prints on flexible films, labels, and cartons remain vibrant and intact throughout the supply chain, including exposure to moisture, handling, and transport.
Signage and Displays: UV-cured prints on signage and displays offer long-lasting visibility and resistance to outdoor elements, making them ideal for both indoor and outdoor applications.
Electronics: In the electronics industry, UV curing is used to secure components and protect circuit boards with durable, conductive inks and coatings.
UV curing is a powerful technology that significantly enhances the durability of prints across various applications. By leveraging the chemical reactions initiated by UV light, this process creates cross-linked polymer structures that are resistant to environmental and mechanical stresses. The rapid curing time, improved adhesion, and enhanced physical properties of UV-cured materials contribute to prints that maintain their quality and integrity over time.
However, achieving optimal results requires a thorough understanding of the curing process, careful selection of materials, and precise control over curing parameters. By considering these factors and tailoring the UV curing process to specific application needs, printers can produce durable, high-quality prints that stand the test of time. As technology continues to advance, UV curing will undoubtedly remain a cornerstone in the printing industry, driving innovation and ensuring that prints meet the highest standards of durability and performance.